Large-area optical grating manufacturing method based on ultrashort-pulse laser-induction self-assembly feature
An ultra-short pulse laser and pulsed laser technology, applied in diffraction grating and other directions, can solve the problems of splicing error, time cost of difficult processing technology, exposure wavefront deflection, etc., to achieve high cycle accuracy, saving research and development cycle and cost.
- Summary
- Abstract
- Description
- Claims
- Application Information
AI Technical Summary
Problems solved by technology
Method used
Image
Examples
Embodiment
[0073] The technical solution of the present embodiment is as follows:
[0074] A method for fabricating a large-area grating with ultrashort pulse laser-induced self-assembly characteristics, comprising the following steps:
[0075] ①Substrate preparation, selection of functional materials, thin film structure design and thin film preparation;
[0076] ②Pulse laser to process the surface of the material to form a surface grating structure;
[0077] ③In order to speed up the production speed, multiple beams are used to process the grating production materials in parallel;
[0078] ④Transfer of surface grating structure to quartz glass substrate.
[0079] For the selection of functional materials, film structure design and film preparation in the above step ①:
[0080] 1) The selected functional material is metal titanium (Ti);
[0081] 2) The multi-layer structure is as follows: functional film, heat insulation film, reflective film, quartz glass substrate; heat insulation...
PUM
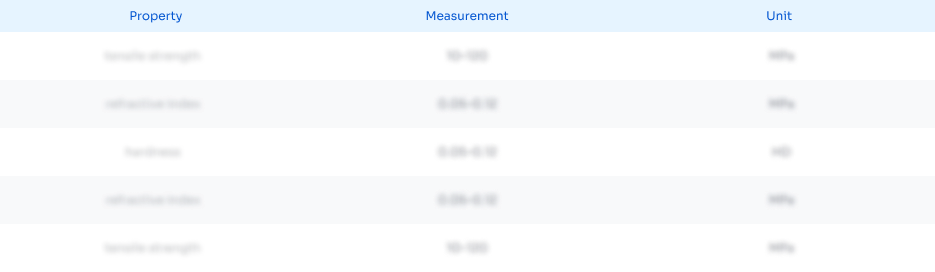
Abstract
Description
Claims
Application Information

- Generate Ideas
- Intellectual Property
- Life Sciences
- Materials
- Tech Scout
- Unparalleled Data Quality
- Higher Quality Content
- 60% Fewer Hallucinations
Browse by: Latest US Patents, China's latest patents, Technical Efficacy Thesaurus, Application Domain, Technology Topic, Popular Technical Reports.
© 2025 PatSnap. All rights reserved.Legal|Privacy policy|Modern Slavery Act Transparency Statement|Sitemap|About US| Contact US: help@patsnap.com