Preparation method for organic phosphorus copolymerized antiflaming polyamide material
A flame retardant and polyamide copolymerization technology, which is applied in the field of flame retardant materials, can solve the problems of large proportion of flame retardant, difficult viscosity of PA6, high cost of raw materials, etc., and achieve the effect of excellent flame retardant performance
- Summary
- Abstract
- Description
- Claims
- Application Information
AI Technical Summary
Problems solved by technology
Method used
Image
Examples
preparation example Construction
[0047] A method for preparing an organophosphorus copolymerized flame-retardant polyamide material, specifically comprising the following steps:
[0048] (1) The flame retardant is reacted with the diamine monomer in advance to prepare a prepolymer.
[0049] Preferably, the flame retardant is or with is a derivative of the matrix;
[0050] where the R 1 and R 2 All are alkylene groups with 1-10 carbon atoms;
[0051] Or one of R1 and R2 is H; X 1 、X 2 H, or 1-4 halogens that can replace H on the benzene ring, such as Br, etc.
[0052] Preferably, the flame retardant and its derivatives are the following:
[0053] R1 is an alkylene group of 1-10 carbon atoms, R2 is H or an alkyl group of 1-10 carbon atoms;
[0054] R1 is an alkylene group of 1-10 carbon atoms, and R2 is an alkylene group of 1-10 carbon atoms;
[0055] R1 and R2 are each an alkylene group of 1-10 carbon atoms, and R3 is an alkyl group of 1-10 carbon atoms;
[0056] R1 and R3 are each an alkyle...
Embodiment 1
[0114] The flame retardant was reacted with hexamethylenediamine to obtain a mixture of No. 1 prepolymer and DDP hexamethylenediamine salt, and the molar ratio of flame retardant to hexamethylenediamine was 1:1.
[0115] Add caprolactam and a catalyst accounting for 1% of the weight of caprolactam into the reactor, vacuumize, fill with nitrogen, and maintain a positive pressure in the reactor; heat the reactor, control the temperature in the reactor to 240°C, and the pressure to 0.3MPa, then start stirring The device continued to stir for 8 hours; reduce the stirring speed, evacuate the reactor to a vacuum degree of -0.05MPa, and then fill it with nitrogen to normal pressure, and then add 1.5% prepolymer of caprolactam weight;
[0116] Vacuum again to -0.05MPa, keep the temperature in the reactor at 240°C, and carry out the copolymerization reaction for 15 minutes; finally fill in nitrogen, control the pressure in the reactor to 0.02MPa, discharge the material, cool, pelletize,...
Embodiment 2
[0119] The flame retardant is reacted with nonanediamine to obtain a mixture of No. 2 prepolymer and flame retardant nonanediamine salt, and the molar ratio of flame retardant to nonanediamine is 1:3.
[0120] Add caprolactam, undecanolactam, hexamethylenediamine with a mass ratio of 1:1:1 and a catalyst of 1% of the total weight of caprolactam, undecanolactam, and hexamethylenediamine into the reactor, vacuumize, fill with nitrogen, and keep The inside of the reactor is under positive pressure;
[0121] Heat the reaction kettle, control the temperature in the reaction kettle to 250°C and the pressure to 0.5MPa, start the stirring device and continue stirring for 7 hours; reduce the stirring speed, evacuate the reaction kettle to a vacuum degree of -0.04MPa and then fill it with nitrogen to normal pressure Add a prepolymer prepared by adding 2% flame retardant equivalent to the sum of the weight of lactam and diamine; evacuate again to a vacuum degree of -0.01MPa, keep the tem...
PUM
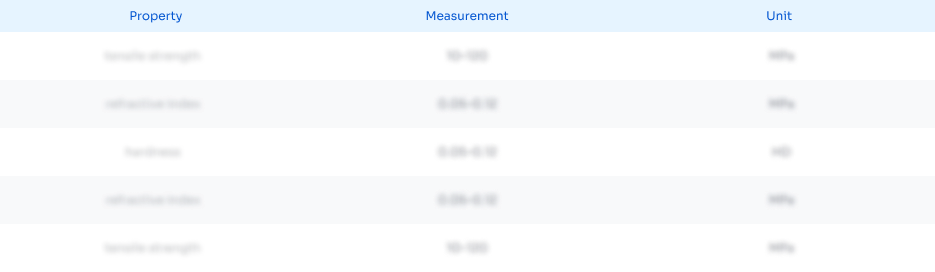
Abstract
Description
Claims
Application Information

- R&D
- Intellectual Property
- Life Sciences
- Materials
- Tech Scout
- Unparalleled Data Quality
- Higher Quality Content
- 60% Fewer Hallucinations
Browse by: Latest US Patents, China's latest patents, Technical Efficacy Thesaurus, Application Domain, Technology Topic, Popular Technical Reports.
© 2025 PatSnap. All rights reserved.Legal|Privacy policy|Modern Slavery Act Transparency Statement|Sitemap|About US| Contact US: help@patsnap.com