Method for preparing polypropylene
A polypropylene and propylene technology, applied in the field of polypropylene preparation, can solve the problems of the influence of copolymerization performance, excessive emptying, small pressure difference in the reactor, etc., and achieve the effects of increasing production load, flexible feeding and wide hydrogen adjustment range
- Summary
- Abstract
- Description
- Claims
- Application Information
AI Technical Summary
Problems solved by technology
Method used
Image
Examples
Embodiment 1
[0035] figure 1 Under the liquid-phase tank parallel flow shown in the figure, TK catalyst, triethylaluminum and methylcyclohexyldimethoxysilane are added in proportion to liquid-phase stirred reactor D201 and liquid-phase stirred reactor D202, Al / Si / Ti is 80 / 5 / 1. The polymerization conditions are as follows: the reaction temperature in the liquid phase stirred reactor D201 and the liquid phase stirred reactor D202 are both 70°C, the reaction pressure is 3.0 MPa, and the catalyst is averaged in the liquid phase stirred reactor D201 and the liquid phase stirred reactor D202. Stay for 30 minutes each; the reaction temperature in the gas-phase fluidized bed reactor D203 is 80°C, the reaction pressure is 1.8MPa, and the residence time of the catalyst is 60 minutes; the reaction temperature in the gas-phase fluidized bed reactor D204 is 70°C, and the reaction pressure is is 1.4MPa, and the catalyst residence time is 65 minutes. The gas-phase hydrogen concentration in the liquid-...
Embodiment 2
[0037] figure 1 Under the liquid-phase tank parallel flow shown in the figure, the TK catalyst, triisobutylaluminum and isobutyltriethoxysilane are respectively added in proportion to the liquid-phase stirred reactor D201 and the liquid-phase stirred reactor D202, Al / Si / Ti is 80 / 5 / 1. The polymerization conditions are as follows: the reaction temperature in the liquid phase stirred reactor D201 and the liquid phase stirred reactor D202 are both 70°C, the reaction pressure is 3.0 MPa, and the catalyst is averaged in the liquid phase stirred reactor D201 and the liquid phase stirred reactor D202. Stay for 30 minutes each; the reaction temperature in the gas-phase fluidized bed reactor D203 is 80°C, the reaction pressure is 1.8MPa, and the residence time of the catalyst is 60 minutes; the reaction temperature in the gas-phase fluidized bed reactor D204 is 70°C, and the reaction pressure is is 1.4MPa, and the catalyst residence time is 65 minutes. The gas-phase hydrogen concentr...
Embodiment 3
[0039] figure 1 Under the parallel flow of liquid phase tanks shown, add TK catalyst in liquid phase stirred reactor D201, add ND catalyst in liquid phase stirred reactor D202, add Cocatalyst triethylaluminum, add external electron donor methylcyclohexyldimethoxysilane in liquid phase stirred reactor D201, external electron donor dicyclopentyl dimethoxysilane in liquid phase stirred reactor D202, two Al / Si / Ti in each liquid phase stirred reactor is 120 / 5 / 1. The polymerization conditions are as follows: the reaction temperature in the liquid phase stirred reactor D201 and the liquid phase stirred reactor D202 are both 70°C, the reaction pressure is 3.0 MPa, and the catalyst is averaged in the liquid phase stirred reactor D201 and the liquid phase stirred reactor D202. Stay for 30 minutes each; the reaction temperature in the gas-phase fluidized bed reactor D203 is 80°C, the reaction pressure is 1.8MPa, and the residence time of the catalyst is 60 minutes; the reaction temperat...
PUM
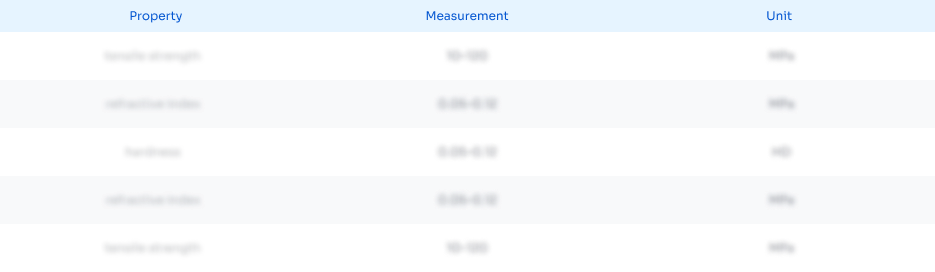
Abstract
Description
Claims
Application Information

- R&D
- Intellectual Property
- Life Sciences
- Materials
- Tech Scout
- Unparalleled Data Quality
- Higher Quality Content
- 60% Fewer Hallucinations
Browse by: Latest US Patents, China's latest patents, Technical Efficacy Thesaurus, Application Domain, Technology Topic, Popular Technical Reports.
© 2025 PatSnap. All rights reserved.Legal|Privacy policy|Modern Slavery Act Transparency Statement|Sitemap|About US| Contact US: help@patsnap.com