Cumyl hydroperoxide and propylene epoxidation method
A technology of cumene hydroperoxide and epoxidation, which is applied in chemical recovery, organic chemistry, etc., can solve the problems of reaction temperature rise and achieve the effect of reducing reaction temperature rise and improving selectivity
- Summary
- Abstract
- Description
- Claims
- Application Information
AI Technical Summary
Problems solved by technology
Method used
Image
Examples
Embodiment 1
[0030] press figure 1 As shown in the technical scheme, the raw material contains a mixture of cumene hydroperoxide with a concentration of 35% by weight, the flow rate is 101166.1 kg / h, the raw material propylene is 10812.7 kg / h, the circulating propylene is 92993.1 kg / h, and the circulation loop of 136648.1 kg / h The oxidation reaction products are mixed, and enter the single-bed adiabatic fixed-bed reactor under the conditions of a reaction temperature of 55°C and a reaction pressure of 3.1MPaG, and mix with Ti / SiO 2 Upon contact with the catalyst, the liquid phase epoxidation reaction generates propylene oxide, dimethylbenzyl alcohol and other by-products. Cumene Hydroperoxide Weight Space Velocity 4.5hr -1 , The molar ratio of total propylene to cumene hydroperoxide is 10.2, the molar ratio of propylene to cumene hydroperoxide at the inlet of the catalyst bed reaches 16.3, and the reactor outlet temperature is 85.8℃. The total conversion rate of benzene was 99.4%, and the m...
Embodiment 2
[0033] Same as [Embodiment 1], only the flow rate of circulating propylene is changed: the circulating propylene flow rate is 61995.4 kg / h, and the others are the same as [Embodiment 1]. Cumene Hydroperoxide Weight Space Velocity 4.5hr -1 , The molar ratio of total propylene to cumene hydroperoxide is 7.1, the molar ratio of propylene to cumene hydroperoxide at the inlet of the catalyst bed reaches 11.2, the reactor outlet temperature is 89.2℃, The total conversion rate of benzene was 99.4%, and the molar selectivity of propylene oxide was 96.0%.
[0034]
Embodiment 3
[0036] Same as [Example 1], only the reactor form is changed: two-bed adiabatic fixed bed reactor, the others are the same as [Example 1]. Cumene Hydroperoxide Weight Space Velocity 4.5hr -1 , The molar ratio of total propylene to cumene hydroperoxide is 10.2, the molar ratio of propylene to cumene hydroperoxide at the inlet of the catalyst bed reaches 16.3, and the reactor outlet temperature is 85.8℃. The total conversion rate of benzene was 99.4%, and the molar selectivity of propylene oxide was 96.2%.
[0037]
PUM
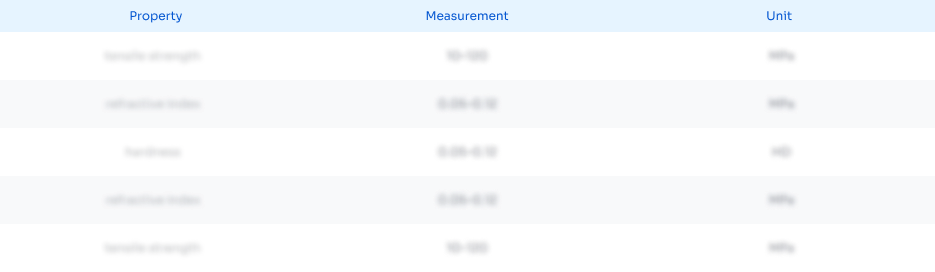
Abstract
Description
Claims
Application Information

- R&D Engineer
- R&D Manager
- IP Professional
- Industry Leading Data Capabilities
- Powerful AI technology
- Patent DNA Extraction
Browse by: Latest US Patents, China's latest patents, Technical Efficacy Thesaurus, Application Domain, Technology Topic, Popular Technical Reports.
© 2024 PatSnap. All rights reserved.Legal|Privacy policy|Modern Slavery Act Transparency Statement|Sitemap|About US| Contact US: help@patsnap.com