Motor rotor pressing plate
A motor rotor and pressure plate technology, applied in the direction of magnetic circuit rotating parts, magnetic circuit shape/style/structure, etc., can solve the problems of cumbersome operation of the rotor pressure plate, accumulation of tolerances in installation, etc., to solve the complicated assembly, prevent grease leakage, The effect of efficient assembly
- Summary
- Abstract
- Description
- Claims
- Application Information
AI Technical Summary
Problems solved by technology
Method used
Image
Examples
Embodiment Construction
[0012] A motor rotor pressure plate, the center of the pressure plate is provided with a mounting shaft hole 1, and the outer circumference of the pressure plate is evenly distributed with pressure plate teeth 4; the upper part of the mounting shaft hole 1 is provided with a positioning keyway 2 for fixed connection with the iron core punch, and the mounting shaft hole 1 Ventilation holes 3 are evenly distributed on the outer circumference of the outer circle; an oil seal labyrinth 5 is provided on the circumference of the pressure plate between the ventilation holes 3 and the installation shaft hole 1, and an annular balance groove 6 is arranged on the periphery of the ventilation hole 3 on the pressure plate .
[0013] The size of the pressing plate teeth 4 provided on the rotor pressing plate is smaller than the supporting iron core teeth, which can avoid interference during the assembly of the rotor squirrel cage.
[0014] The ventilation hole 3 provided on the rotor press...
PUM
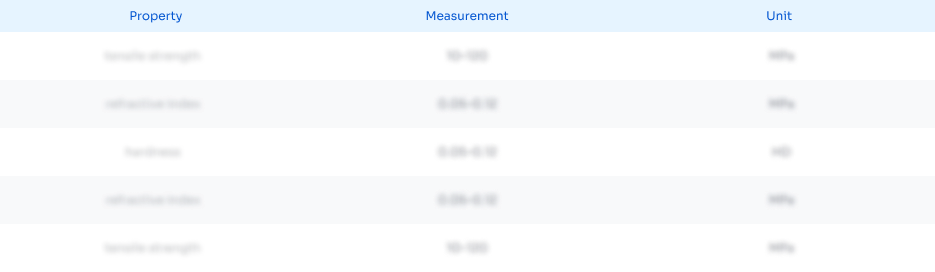
Abstract
Description
Claims
Application Information

- Generate Ideas
- Intellectual Property
- Life Sciences
- Materials
- Tech Scout
- Unparalleled Data Quality
- Higher Quality Content
- 60% Fewer Hallucinations
Browse by: Latest US Patents, China's latest patents, Technical Efficacy Thesaurus, Application Domain, Technology Topic, Popular Technical Reports.
© 2025 PatSnap. All rights reserved.Legal|Privacy policy|Modern Slavery Act Transparency Statement|Sitemap|About US| Contact US: help@patsnap.com