Filtering tank capable of fully filter-pressing waste oil
A filter tank and filter screen technology, applied in the field of filter tanks, can solve the problems of oil waste, waste oil filtration loss, unfavorable storage, etc., and achieve the effects of avoiding low efficiency, improving oil recovery rate, and avoiding difficulties
- Summary
- Abstract
- Description
- Claims
- Application Information
AI Technical Summary
Problems solved by technology
Method used
Image
Examples
Embodiment 1
[0020] Such as figure 1 and figure 2 As shown, this embodiment includes a closed tank body 1, and also includes a rotary filter 2, the rotary filter 2 is installed in the tank body 1 through a rotating shaft 5 including an oil outlet, and the outer layer of the rotary filter 2 is The filter screen 21, the inner layer of the rotary filter 2 is a cylinder 22, and the rotating shaft 5 is fixedly connected to the two sides of the cylinder 22 along the center of rotation. area, the percolation area is divided into a plurality of isolated filtration zones 24 by a partition block 23, and each filter zone 24 is equipped with an oil outlet branch pipe 4 with a control valve, and all the oil outlet branch pipes 4 with a control valve are connected to the center of the rotating shaft 5 An oil outlet, an oil inlet pipe 10 and a pressurized air pipe 11 are arranged on the tank body 1 .
[0021] In order to further improve the recovery rate of waste oil and increase the filtering surface...
Embodiment 2
[0024] Such as image 3 As shown, the difference between Embodiment 2 and Embodiment 1 is that a helical blade 9 is installed on the cylindrical surface of the rotary filter 2 . The effect of spiral blade 9 is to promote the waste residue at the bottom of the filter tank. When the rotary filter 2 rotates, the spiral blade 9 pushes the waste residue to one side of the tank body to realize slag removal.
PUM
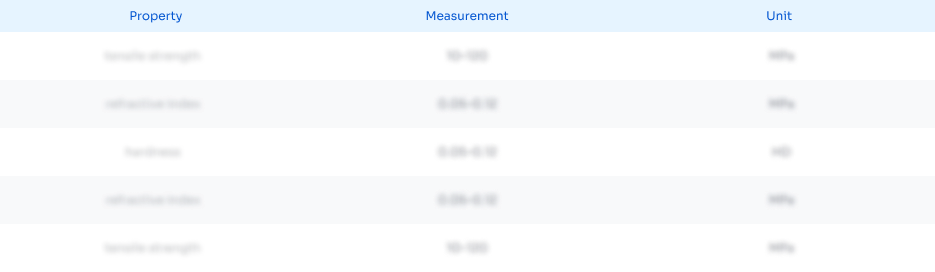
Abstract
Description
Claims
Application Information

- Generate Ideas
- Intellectual Property
- Life Sciences
- Materials
- Tech Scout
- Unparalleled Data Quality
- Higher Quality Content
- 60% Fewer Hallucinations
Browse by: Latest US Patents, China's latest patents, Technical Efficacy Thesaurus, Application Domain, Technology Topic, Popular Technical Reports.
© 2025 PatSnap. All rights reserved.Legal|Privacy policy|Modern Slavery Act Transparency Statement|Sitemap|About US| Contact US: help@patsnap.com