A Method of Quickly Extracting the Internal Load of the Kinematic Mechanism and Optimizing the Design Scheme
A motion mechanism and design scheme technology, applied in computing, special data processing applications, instruments, etc., can solve problems such as increased design costs and extended design cycles, and achieve the effect of occupying less computer memory resources, reducing design costs, and powerful functions
- Summary
- Abstract
- Description
- Claims
- Application Information
AI Technical Summary
Problems solved by technology
Method used
Image
Examples
Embodiment Construction
[0073] The specific implementation process of the present invention will be further described in detail below in conjunction with the accompanying drawings. Its basic implementation process is as follows:
[0074] Taking a certain kinematic mechanism as an example, the content and steps of the method and tool for quickly extracting the internal load of the kinematic mechanism and preliminary optimization of the design plan are explained. The drawings are all taken from the analysis tool of a certain kinematic mechanism. The internal load extraction of this kinematic mechanism And the preliminary optimization of the scheme all adopted the present invention.
[0075] Step 1: Establish a schematic diagram of the kinematic mechanism under the kinematic mechanism reference coordinate system;
[0076] Step 2, establishing the load conditions required for the analysis and optimization of the kinematic mechanism;
[0077] The load cases in the kinematic mechanism include:
[0078] ...
PUM
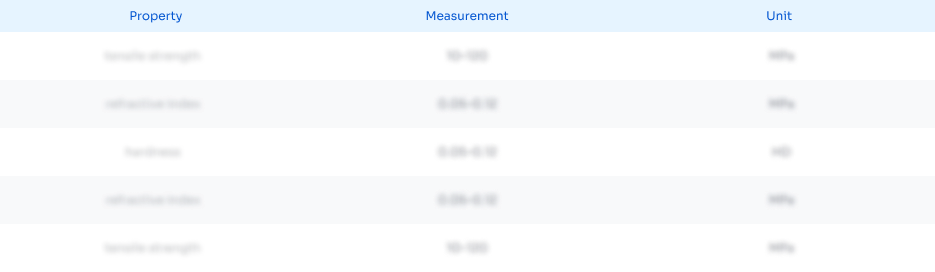
Abstract
Description
Claims
Application Information

- Generate Ideas
- Intellectual Property
- Life Sciences
- Materials
- Tech Scout
- Unparalleled Data Quality
- Higher Quality Content
- 60% Fewer Hallucinations
Browse by: Latest US Patents, China's latest patents, Technical Efficacy Thesaurus, Application Domain, Technology Topic, Popular Technical Reports.
© 2025 PatSnap. All rights reserved.Legal|Privacy policy|Modern Slavery Act Transparency Statement|Sitemap|About US| Contact US: help@patsnap.com