Laminated Radial Hybrid Compliant Actuator
A laminated, radiation-type technology, applied in the direction of generators/motors, piezoelectric effect/electrostrictive or magnetostrictive motors, electrical components, etc., can solve the problem of strong bearing capacity of parallel compliant mechanisms and large packaging volume. , high-frequency noise and other problems, to achieve the effect of high mechanical bearing capacity, wide working bandwidth and light weight
- Summary
- Abstract
- Description
- Claims
- Application Information
AI Technical Summary
Problems solved by technology
Method used
Image
Examples
Embodiment Construction
[0028] The embodiments of the present invention will be described in detail below in conjunction with the accompanying drawings. This embodiment is implemented on the premise of the technical solution of the present invention, and detailed implementation methods and specific operating procedures are provided, but the protection scope of the present invention is not limited to the following Example.
[0029] Please refer to figure 1 and figure 2 , as shown in the figure, the stacked radial type hybrid compliance driver includes a stacked hybrid compliance amplification mechanism 1 and a stacked piezoelectric ceramic sheet 2 .
[0030] The laminated hybrid compliant amplifying mechanism 1 can convert radial input displacement into axial output displacement. The shape of the laminated hybrid compliant amplifying mechanism is disc-shaped, and the internal functional structure is radially symmetrical to the center of rotation. The laminated hybrid compliant amplifying mechanism ...
PUM
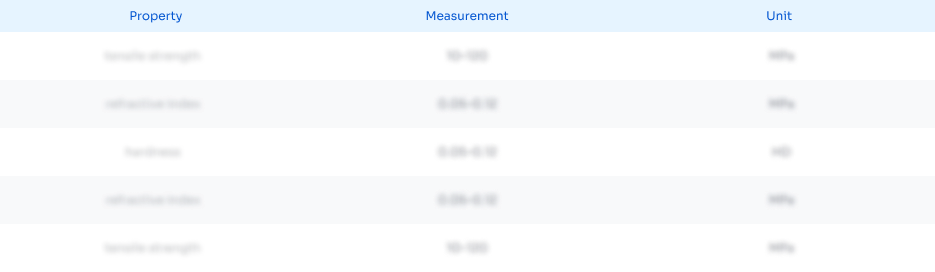
Abstract
Description
Claims
Application Information

- Generate Ideas
- Intellectual Property
- Life Sciences
- Materials
- Tech Scout
- Unparalleled Data Quality
- Higher Quality Content
- 60% Fewer Hallucinations
Browse by: Latest US Patents, China's latest patents, Technical Efficacy Thesaurus, Application Domain, Technology Topic, Popular Technical Reports.
© 2025 PatSnap. All rights reserved.Legal|Privacy policy|Modern Slavery Act Transparency Statement|Sitemap|About US| Contact US: help@patsnap.com