Electromagnetic clamping mechanism and linear driving device and combination with same
A clamping device and linear drive technology, applied in the direction of generators/motors, electrical components, etc., can solve the problems of small deformation of the clamp, loss of clamping function, and impossibility of realization, etc., to achieve sensitive motion control, fewer components, The effect of simple structure
- Summary
- Abstract
- Description
- Claims
- Application Information
AI Technical Summary
Problems solved by technology
Method used
Image
Examples
Embodiment 1
[0071] This embodiment provides the electromagnetic clamping mechanism of the first structure, including an electromagnet, a permanent magnet and a deformation body, the magnetic poles of the permanent magnets are in direct contact with or close to the magnetic poles of the electromagnet to form a control magnetic circuit, and the deformation body It is rigidly connected with the permanent magnet; the permanent magnet moves relative to the electromagnet under the drive of the magnetic field of the control magnetic circuit, and drives the deformable body to deform, thereby realizing clamp locking and release.
[0072] Specifically:
[0073] There are two permanent magnets 112, which are respectively arranged on the magnetic link of the electromagnet 111. A control magnetic circuit is formed between the two permanent magnets 112 and the electromagnet 111 located in the middle position, and the deformation body 113 is rigidly connected with the permanent magnet 112. In this embod...
Embodiment 2
[0080] This embodiment provides the electromagnetic clamping mechanism of the second structure, which has the same working principle as the electromagnetic clamping mechanism provided in Embodiment 1. The difference from Embodiment 1 is that there are two deformation bodies Correspondingly, there are two sets of permanent magnet electromagnetic combinations for driving the two shrapnels for the pre-tensioned shrapnel with matching bayonet.
[0081] Specifically:
[0082] Each group of permanent magnet electromagnetic combination all comprises: two permanent magnets 122 are arranged on the magnetic link of electromagnet 121 respectively, and form control magnetic circuit with electromagnet 121, further, between electromagnet 121 and permanent magnet 122 It is also coaxially arranged on the moving shaft 124; the outer ends of the two permanent magnets 122 are respectively provided with rigid material bodies, and the two ends of the deformable body 123 are fixedly connected with ...
Embodiment 3
[0087] This embodiment provides the electromagnetic clamping mechanism of the third structure, and the electromagnetic clamping mechanism has the same working principle as that of Embodiment 1. The difference from Embodiment 1 is that the deformed body used in this embodiment is a hand pliers Structural variants.
[0088] Such as image 3 Shown in (a), it is the deformed body 133 of the hand pliers structure of the first structure. The two V-shaped elastic bodies that constitute the deformed body 133 of the hand pliers mechanism are symmetrically arranged and connected axially. When the permanent magnet 132 is opposite to the electromagnet 131 When moving away, push the lower end of the pliers structure deformation body 133 away. Correspondingly, the upper end of the hand pliers structure deformation body 133 approaches and finally locks under the driving force to realize the clamping and locking state.
[0089] Such as image 3 As shown in (b), it is the deformed body of th...
PUM
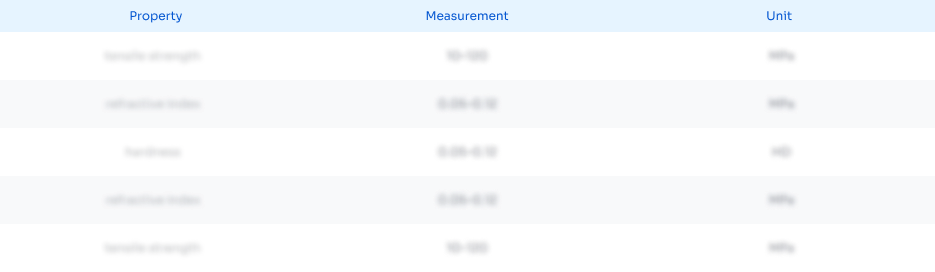
Abstract
Description
Claims
Application Information

- R&D Engineer
- R&D Manager
- IP Professional
- Industry Leading Data Capabilities
- Powerful AI technology
- Patent DNA Extraction
Browse by: Latest US Patents, China's latest patents, Technical Efficacy Thesaurus, Application Domain, Technology Topic, Popular Technical Reports.
© 2024 PatSnap. All rights reserved.Legal|Privacy policy|Modern Slavery Act Transparency Statement|Sitemap|About US| Contact US: help@patsnap.com