Connecting sleeve parison tube double-sided milling machine
A technology for connecting sleeves and blank tubes, applied in the field of machinery, can solve problems such as low efficiency, insufficient smoothness, and texture generation
- Summary
- Abstract
- Description
- Claims
- Application Information
AI Technical Summary
Problems solved by technology
Method used
Image
Examples
Embodiment Construction
[0018] The present invention will be further described below. The device includes a base, a feeding mechanism, a clamping mechanism and a knife-feeding mechanism:
[0019] Such as figure 1 , figure 2 and image 3 As shown, the base 1 is a rectangular three-dimensional support, and the feeding mechanism is located above the middle of the base 1, including an inclined feeding track 19, in which the connecting sleeve blank tube can be placed, and the connecting sleeve blank tube can slide downward by its own gravity. The bottom of the feeding track 19 is connected with the discharge port 40, and a connecting rod 25 is installed on the outside of the discharge port 40, which is inclined downward. The connecting rod 25 is covered with an elastic clamping plate 26, and the connecting rod 25 is covered with a spring 41 to support the discharge. Between the outer wall of the opening 40 and the elastic clamping plate 26, the lower end of the elastic clamping plate 26 is located belo...
PUM
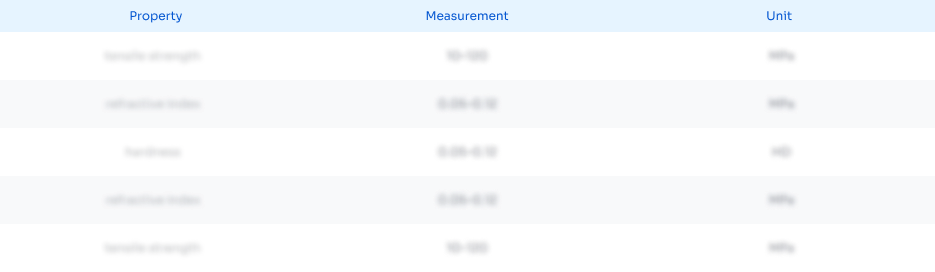
Abstract
Description
Claims
Application Information

- R&D Engineer
- R&D Manager
- IP Professional
- Industry Leading Data Capabilities
- Powerful AI technology
- Patent DNA Extraction
Browse by: Latest US Patents, China's latest patents, Technical Efficacy Thesaurus, Application Domain, Technology Topic, Popular Technical Reports.
© 2024 PatSnap. All rights reserved.Legal|Privacy policy|Modern Slavery Act Transparency Statement|Sitemap|About US| Contact US: help@patsnap.com