Vacuum clamp for centering optical element in machining process
A technology of optical components and vacuum clips, which is applied in the direction of optical components, optics, manufacturing tools, etc., can solve the problems of chipping and damage of components, and achieve the effect of fast centering and avoiding chipping and damage of components
- Summary
- Abstract
- Description
- Claims
- Application Information
AI Technical Summary
Problems solved by technology
Method used
Image
Examples
Embodiment Construction
[0019] The present invention will be described in further detail below in conjunction with the accompanying drawings and specific embodiments.
[0020] Such as figure 2 with image 3 As shown, a vacuum fixture for processing and centering an optical element, the fixture includes an optical element 1, a vacuum fixture body 2, a sealing ring 3 and a protective layer 4, and the center of the vacuum fixture body 2 is provided with an air pumping center hole 21 , the upper surface of the vacuum chuck body 2 is provided with a support surface 22, the support surface 22 is provided with an annular groove 23, the sealing ring 3 is arranged in the annular groove 23, the protective layer 4 is arranged on the support surface 22, the optical element 1 Set on the protective layer 4; the fixture also includes an adjustment bracket 5, a screw 6 and a differential nut 7, the adjustment bracket 5 is fixed on the side of the vacuum clamp body 2 through the screw 6, and the differential nut 7 ...
PUM
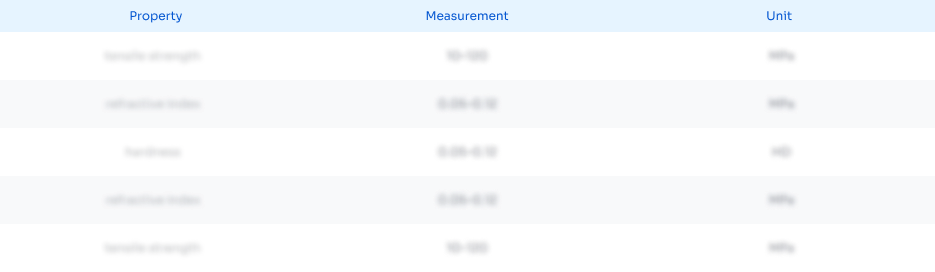
Abstract
Description
Claims
Application Information

- R&D
- Intellectual Property
- Life Sciences
- Materials
- Tech Scout
- Unparalleled Data Quality
- Higher Quality Content
- 60% Fewer Hallucinations
Browse by: Latest US Patents, China's latest patents, Technical Efficacy Thesaurus, Application Domain, Technology Topic, Popular Technical Reports.
© 2025 PatSnap. All rights reserved.Legal|Privacy policy|Modern Slavery Act Transparency Statement|Sitemap|About US| Contact US: help@patsnap.com