Filter material, filter element, filter module and machining method thereof
A filter material and filter module technology, applied in the fields of filtration and separation, separation methods, chemical instruments and methods, etc., can solve the problems of small air output, poor ventilation effect, inability to remove air odor, etc., and achieve high environmental protection effect.
- Summary
- Abstract
- Description
- Claims
- Application Information
AI Technical Summary
Problems solved by technology
Method used
Image
Examples
Embodiment 1
[0025] The filter material includes rattan core, rattan bark and poplar wood. The proportion of rattan bark is between 20% and 60%, the proportion of rattan core is between 30% and 50%, and the proportion of poplar wood particles is between 20% and 60%. Between 30%.
[0026] The first step is to separate the rattan bark and rattan core from the rattan. The rattan bark is made into plant fibers through processes including separation, opening, activation, and swelling. The rattan core and poplar are crushed into granules for future use.
[0027] In the second step, the plant fibers and granules obtained from rattan bark, rattan core and poplar are mixed with water and stirred to dissolve each other, and then dehydrated by a centrifuge.
[0028] In the third step, the dehydrated material is made into a fiber cloth through a process including layering and rolling, and a filter module is obtained after molding and cutting.
Embodiment 2
[0030] The filter material includes rattan core, rattan bark and poplar wood. The proportion of rattan bark is between 20% and 60%, the proportion of rattan core is between 30% and 50%, and the proportion of poplar wood particles is between 20% and 60%. Between 30%.
[0031] The first step is to separate the rattan bark and rattan core from the rattan. The rattan bark is made into plant fibers through processes including separation, opening, activation, and swelling. The rattan core and poplar are crushed into granules for future use.
[0032] In the second step, the plant fibers and granules obtained from rattan bark, rattan core and poplar are mixed with water and stirred to dissolve each other, and then dehydrated by a centrifuge.
[0033] In the third step, the dehydrated material is added with at least 30% cellulose acetate to the mixture to obtain a microfiltration filter material, which is made into a fiber cloth through a process including layering and rolling, and is ...
Embodiment 3
[0035] The filter material includes rattan core, rattan bark and poplar wood. The proportion of rattan bark is between 20% and 60%, the proportion of rattan core is between 30% and 50%, and the proportion of poplar wood particles is between 20% and 60%. Between 30%.
[0036] The first step is to separate the rattan bark and rattan core from the rattan. The rattan bark is made into plant fibers through processes including separation, opening, activation, and swelling. The rattan core and poplar are crushed into granules for future use.
[0037] In the second step, the mixture of plant fibers and granules obtained from rattan bark, rattan core and poplar is added to the mixture with 30% cellulose acetate, mixed with water, stirred and dissolved, and then dehydrated by a centrifuge.
[0038] In the third step, the dehydrated material is obtained as a microfiltration filter material, which is made into a fiber cloth through a process including layer laying and rolling, and a filte...
PUM
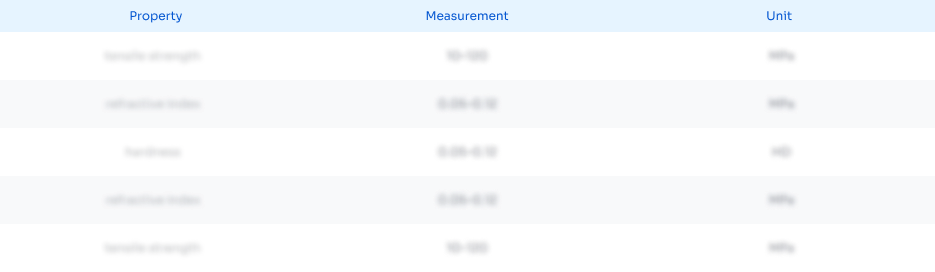
Abstract
Description
Claims
Application Information

- R&D
- Intellectual Property
- Life Sciences
- Materials
- Tech Scout
- Unparalleled Data Quality
- Higher Quality Content
- 60% Fewer Hallucinations
Browse by: Latest US Patents, China's latest patents, Technical Efficacy Thesaurus, Application Domain, Technology Topic, Popular Technical Reports.
© 2025 PatSnap. All rights reserved.Legal|Privacy policy|Modern Slavery Act Transparency Statement|Sitemap|About US| Contact US: help@patsnap.com