Low-manganese cast grinding ball
A casting grinding ball, a low-level technology, applied in the field of casting grinding balls, can solve problems such as uneven hardness, increased production cost of casting grinding balls, insufficient hardenability, etc., to improve hardenability, optimize composition and heat treatment process, improve The effect of the tempering effect
- Summary
- Abstract
- Description
- Claims
- Application Information
AI Technical Summary
Problems solved by technology
Method used
Examples
Embodiment 1
[0020] Prepare as follows:
[0021] S1: Weighing each raw material according to the mass fraction, casting and molding after smelting to obtain a semi-finished product of cast grinding ball;
[0022] S2: Put the semi-finished product of the grinding ball obtained in S1 into the furnace and heat it up to 520°C for 150 minutes, heat it up to 750°C for 150 minutes, heat it up to 920°C for 150 minutes, heat it up to 1000°C for 150 minutes, and heat it at an oil temperature of 100°C. Oil quenching was carried out in the quenching oil, and the quenching time was 8 minutes. After oil quenching, it was placed in a holding furnace at a heating rate of 60 ℃ / h from room temperature to 350 ℃ for 480 minutes, and then slowly cooled to room temperature for 460 minutes to obtain cast grinding balls.
Embodiment 2
[0024] Prepare as follows:
[0025] S1: Weighing each raw material according to the mass fraction, casting and molding after smelting to obtain a semi-finished product of cast grinding ball;
[0026] S2: Put the semi-finished product of the grinding ball obtained in S1 into the furnace and heat it up to 530°C for 140 minutes, then heat it up to 760°C for 140 minutes, heat it up to 960°C for 140 minutes, heat it up to 1040°C for 140 minutes, and heat it at an oil temperature of 120°C. Oil quenching was carried out in the quenching oil, and the quenching time was 14 minutes. After oil quenching, it was put into a holding furnace at a heating rate of 100 ℃ / h from room temperature to 380 ℃ for 470 minutes, and then slowly cooled to room temperature for 470 minutes to obtain cast balls.
Embodiment 3
[0028] Prepare as follows:
[0029] S1: Weighing each raw material according to the mass fraction, casting and molding after smelting to obtain a semi-finished product of cast grinding ball;
[0030] S2: Put the semi-finished product of the grinding ball obtained in S1 into the furnace and heat it up to 510°C for 160 minutes, then heat it up to 740°C for 160 minutes, heat it up to 880°C for 140 minutes, heat it up to 970°C for 140 minutes, and heat it at an oil temperature of 75°C. Oil quenching was carried out in the quenching oil for 3 minutes. After oil quenching, it was placed in a holding furnace at a rate of 20°C / h from room temperature to 300°C for 490 minutes, and then slowly cooled to room temperature for 450 minutes to obtain cast grinding balls.
[0031] In Examples 1-3, various properties of the prepared cast grinding balls were tested, and the performance data are shown in Table 2.
[0032]
[0033] The data in the above table 2 shows that the cast gr...
PUM
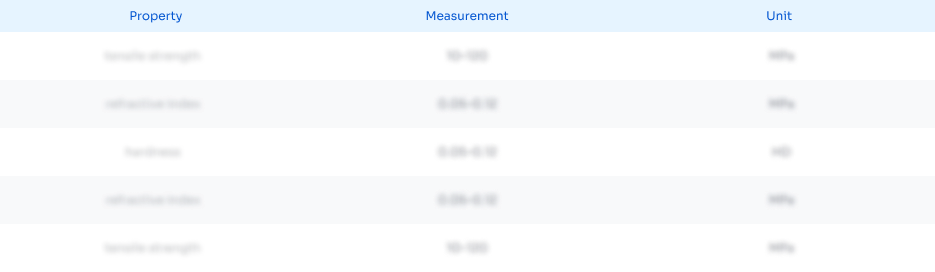
Abstract
Description
Claims
Application Information

- R&D Engineer
- R&D Manager
- IP Professional
- Industry Leading Data Capabilities
- Powerful AI technology
- Patent DNA Extraction
Browse by: Latest US Patents, China's latest patents, Technical Efficacy Thesaurus, Application Domain, Technology Topic, Popular Technical Reports.
© 2024 PatSnap. All rights reserved.Legal|Privacy policy|Modern Slavery Act Transparency Statement|Sitemap|About US| Contact US: help@patsnap.com