Piezoelectric tuning mechanism
A tuning mechanism and piezoelectric technology, applied in the field of tuning mechanism, can solve the problems of huge servo control system, low tuning speed, and not too high tuning frequency, and achieve high frequency/frequency locking accuracy, high electromechanical conversion efficiency, and position repetition good sex effect
- Summary
- Abstract
- Description
- Claims
- Application Information
AI Technical Summary
Problems solved by technology
Method used
Image
Examples
Embodiment Construction
[0015] The piezoelectric tuning mechanism includes piezoelectric ceramics and a displacement amplifier, and the displacement amplifier is roughly " ” shape, the displacement amplifier includes an elastic part and a supporting part, figure 1 Middle 3 is the elastic part, made of elastic alloy, figure 1 Middle 2 is the support part, which is made of low-expansion alloy, the expansion coefficient of the elastic alloy is greater than that of the piezoelectric ceramic, and the piezoelectric ceramic is fixedly connected to the two opposite sides of the displacement amplifier, so that the piezoelectric tuning Organizations roughly "Shape, the two sides fixedly connected by piezoelectric ceramics in the displacement amplifier of the piezoelectric tuning mechanism are elastic parts made of elastic alloy materials. By adjusting the length of the elastic part and the supporting part, the comprehensive expansion of the displacement amplifier can be adjusted Coefficient, so that the co...
PUM
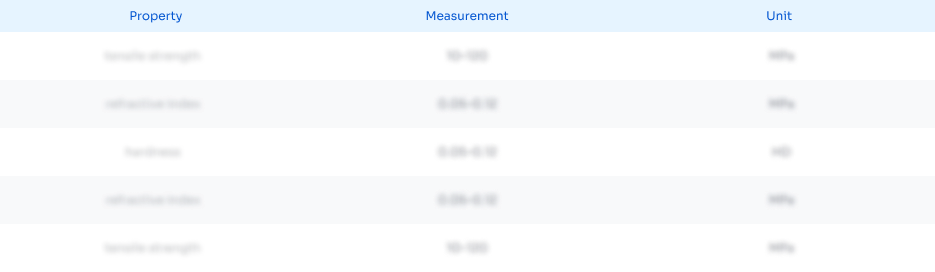
Abstract
Description
Claims
Application Information

- Generate Ideas
- Intellectual Property
- Life Sciences
- Materials
- Tech Scout
- Unparalleled Data Quality
- Higher Quality Content
- 60% Fewer Hallucinations
Browse by: Latest US Patents, China's latest patents, Technical Efficacy Thesaurus, Application Domain, Technology Topic, Popular Technical Reports.
© 2025 PatSnap. All rights reserved.Legal|Privacy policy|Modern Slavery Act Transparency Statement|Sitemap|About US| Contact US: help@patsnap.com