Distillate oil hydrotreatment process
A technology of hydroprocessing and hydrogen, which is applied in the fields of hydroprocessing process, petroleum industry, and hydrocarbon oil treatment, etc. It can solve the problems of increasing the investment cost of reactors, etc., and achieve the effects of improving hydrogen dissolving capacity, simple process flow and stable operation
- Summary
- Abstract
- Description
- Claims
- Application Information
AI Technical Summary
Problems solved by technology
Method used
Image
Examples
Embodiment 1
[0041] The reforming raw material goes through the heating furnace to reach the required temperature and fully mixes and dissolves the hydrogen in the gas-liquid mixer, and then enters the first hydrogenation reactor. The reaction conditions are: reaction system pressure 1.1MPa, reaction temperature 251°C, converted hydrogen oil volume The ratio is 110:1, part of the effluent is recycled to the inlet of each reactor, the circulation ratio is 5:1, and part of it enters the second hydrogenation reactor. The reaction conditions are: reaction system pressure 1.1MPa, reaction temperature 240°C, converted hydrogen oil volume The ratio is 100:1, part of the effluent is circulated to the inlet of each reactor, the circulation ratio is 5:1, and part of it enters the first separator for gas-liquid separation, and the separated liquid effluent enters the storage tank 19. The raw material oil properties and product properties are listed in Table 2.
[0042] It can be seen from Table 2 tha...
Embodiment 2
[0044] The mixed diesel raw material goes through the heating furnace to reach the required temperature and is fully mixed and dissolved with hydrogen in the gas-liquid mixer before entering the first hydrogenation reactor. The ratio is 260:1, part of the effluent is recycled to the inlet of each reactor, the circulation ratio is 3:1, and part of it enters the second hydrogenation reactor. The reaction conditions are: reaction system pressure 6.2MPa, reaction temperature 300°C, converted hydrogen oil volume The ratio is 260:1, part of the effluent is recycled to the inlet of each reactor, the circulation ratio is 3:1, and part of it enters the first separator for gas-liquid separation, and the separated liquid effluent enters the storage tank 19. The raw material oil properties and product properties are listed in Table 3.
[0045] It can be seen from Table 3 that the sulfur and nitrogen content in the blended diesel can be significantly reduced by using this technology.
Embodiment 3
[0047] The middle base heavy distillate oil (mixed with coking wax oil) goes through the heating furnace to reach the required temperature and fully mixes and dissolves with hydrogen in the gas-liquid mixer, and then enters the first hydrogenation reactor. The reaction conditions are: the pressure of the reaction system is 14.0MPa , The reaction temperature is 380°C, the converted hydrogen to oil volume ratio is 300:1, a part of the effluent is recycled to the inlet of each reactor, the circulation ratio is 2:1, and part of it enters the second hydrogenation reactor; the reaction conditions are: reaction system pressure 14.0MPa , The reaction temperature is 378°C, the converted hydrogen-oil volume ratio is 300:1, part of the effluent is recycled to the inlet of each reactor, and the circulation ratio is 2:1, and part of it enters the first separator for gas-liquid separation, and the separated liquid effluent enters storage tank19. The raw material oil properties and product p...
PUM
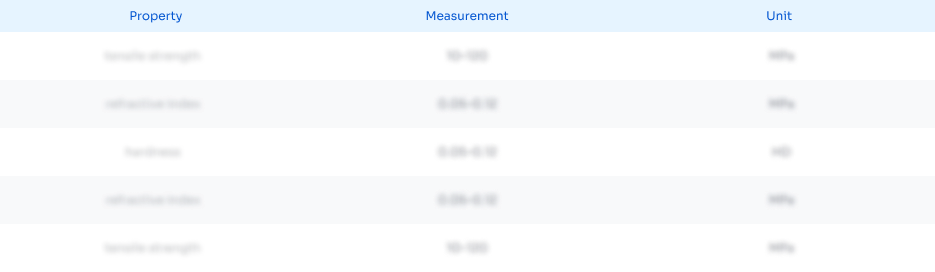
Abstract
Description
Claims
Application Information

- R&D
- Intellectual Property
- Life Sciences
- Materials
- Tech Scout
- Unparalleled Data Quality
- Higher Quality Content
- 60% Fewer Hallucinations
Browse by: Latest US Patents, China's latest patents, Technical Efficacy Thesaurus, Application Domain, Technology Topic, Popular Technical Reports.
© 2025 PatSnap. All rights reserved.Legal|Privacy policy|Modern Slavery Act Transparency Statement|Sitemap|About US| Contact US: help@patsnap.com