Hydraulically-controlled demolition robot in intense-radiation environment
A technology for dismantling robots and radiation environments, applied to manipulators, manufacturing tools, etc., can solve the problems of difficult to form a support surface, the robot is turned over, and the outrigger mechanism is complicated, so as to reduce the difficulty of processing and installation, and simplify installation and maintenance. The effect of convenient daily maintenance
- Summary
- Abstract
- Description
- Claims
- Application Information
AI Technical Summary
Problems solved by technology
Method used
Image
Examples
Embodiment Construction
[0017] Hereinafter, the invention will now be described more fully with reference to the accompanying drawings, in which various embodiments are shown. However, this invention may be embodied in many different forms and should not be construed as limited to the embodiments set forth herein. Rather, these embodiments are provided so that this disclosure will be thorough and complete, and will fully convey the scope of the invention to those skilled in the art.
[0018] Hereinafter, exemplary embodiments of the present invention will be described in more detail with reference to the accompanying drawings.
[0019] Reference attached figure 1 , is a schematic diagram of the structure of the hydraulically controlled demolition robot.
[0020] 1. Anti-nuclear hardening
[0021] Since the hydraulic control demolition robot has to work for a long time in a nuclear radiation environment, it is necessary to protect its electrical control system and the circuit control module of the ...
PUM
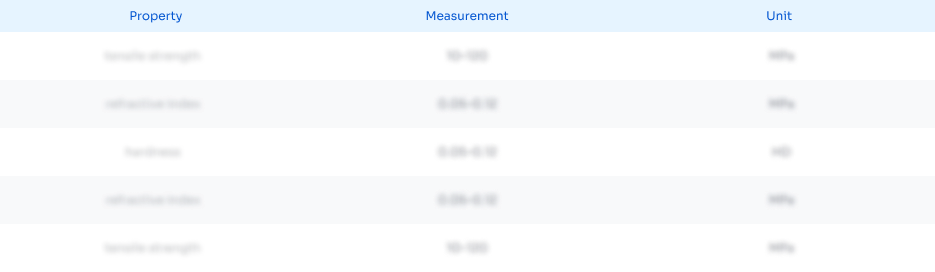
Abstract
Description
Claims
Application Information

- Generate Ideas
- Intellectual Property
- Life Sciences
- Materials
- Tech Scout
- Unparalleled Data Quality
- Higher Quality Content
- 60% Fewer Hallucinations
Browse by: Latest US Patents, China's latest patents, Technical Efficacy Thesaurus, Application Domain, Technology Topic, Popular Technical Reports.
© 2025 PatSnap. All rights reserved.Legal|Privacy policy|Modern Slavery Act Transparency Statement|Sitemap|About US| Contact US: help@patsnap.com