Joint of multi-section folding type remote operation mechanical arm
A technology of teleoperation and robotic arm, which is applied in the field of joints of robotic arms. It can solve the problems of cumbersome installation and replacement of joint position sensors, low stiffness, and reduced precision of joint modules, and achieve the effects of increased stiffness, simple and convenient operation, and simple detection.
- Summary
- Abstract
- Description
- Claims
- Application Information
AI Technical Summary
Problems solved by technology
Method used
Image
Examples
Embodiment 1
[0024] figure 1 The front view of the joint structure of the multi-section folding teleoperated manipulator of the present invention is given, figure 2 It is a three-dimensional schematic diagram of the joint structure of the present invention, image 3 for figure 1 Schematic diagram of cut-away in direction A.
[0025] to combine Figure 1 to Figure 3 , the joint of this multi-section folding remote-operated mechanical arm in this embodiment includes: joint shaft 13, joint wheel 14, motor 15, flange 16, driving wheel 17, fixed pulley 18, steel wire cable 19, bracket 20 , Pull wire sensor 21, each joint is driven by a motor 15, the motor 15 is fixedly installed inside the joint arm through the flange 16, one side of the output shaft of the motor 15 is close to the corresponding joint wheel 14, and the driving wheel 17 is fixed at the output of the motor 15 At the shaft end, the axis of the output shaft of the motor 15 is parallel to the central axis of the joint arm. The ...
PUM
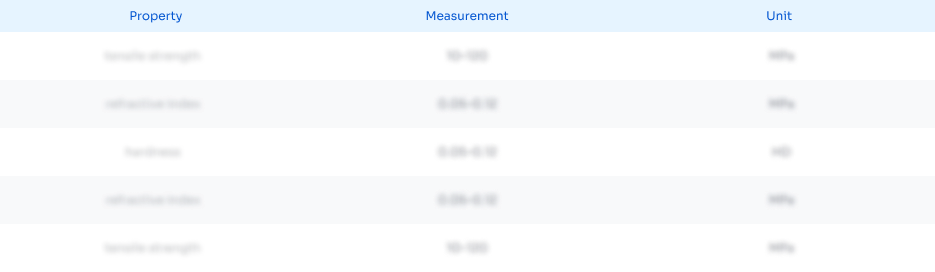
Abstract
Description
Claims
Application Information

- Generate Ideas
- Intellectual Property
- Life Sciences
- Materials
- Tech Scout
- Unparalleled Data Quality
- Higher Quality Content
- 60% Fewer Hallucinations
Browse by: Latest US Patents, China's latest patents, Technical Efficacy Thesaurus, Application Domain, Technology Topic, Popular Technical Reports.
© 2025 PatSnap. All rights reserved.Legal|Privacy policy|Modern Slavery Act Transparency Statement|Sitemap|About US| Contact US: help@patsnap.com