Remote displacement measurement system based on position sensor
A technology of displacement measurement and displacement sensor, which is applied in the direction of measuring devices, instruments, and optical devices, etc. It can solve the problems of being easily disturbed by environmental factors and low detection accuracy of feedback optical signals, and achieves simple installation and debugging process and improved reliability. , The effect of improving the measurement accuracy
- Summary
- Abstract
- Description
- Claims
- Application Information
AI Technical Summary
Problems solved by technology
Method used
Image
Examples
Embodiment Construction
[0021] This embodiment utilizes that the horizontal section of the cubic prism is a rectangle. In this embodiment, a fixed plane of the cubic prism is arranged on the base, and the other three planes that are sequentially connected clockwise are the first transmission surface, the incident surface and the second plane. transmissive surface.
[0022] Such as figure 1 As shown, the embodiment includes a telescopic (mirror) part, wherein an objective lens group 16 and an eyepiece group 17 form an optical axis along the focal length of the lens, and also includes a first cube prism 11, a second cube prism 12, a laser emitter 15 and a PSD displacement Sensor 01, the incident surface 11b of the first cubic prism 11 is perpendicular to the incident surface 12b of the second cubic prism 12; the first transmission surface 11a and the second transmission surface 11c of the first cubic prism 11, and the incidence Face 12b is coaxial with the fixed plane, and the incident face 12b of the...
PUM
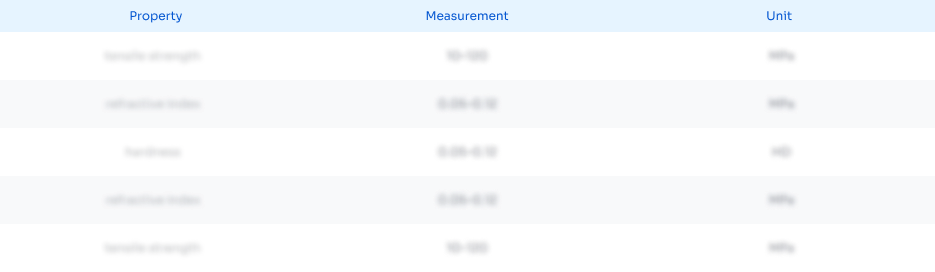
Abstract
Description
Claims
Application Information

- R&D
- Intellectual Property
- Life Sciences
- Materials
- Tech Scout
- Unparalleled Data Quality
- Higher Quality Content
- 60% Fewer Hallucinations
Browse by: Latest US Patents, China's latest patents, Technical Efficacy Thesaurus, Application Domain, Technology Topic, Popular Technical Reports.
© 2025 PatSnap. All rights reserved.Legal|Privacy policy|Modern Slavery Act Transparency Statement|Sitemap|About US| Contact US: help@patsnap.com