Vibration fault detection system and method for wind turbine generator units
A technology for wind turbines and fault detection, applied in measuring devices, measuring ultrasonic/sonic/infrasonic waves, instruments, etc., can solve the problems of long time consumption and low monitoring efficiency, and achieve the effect of saving time, obvious advantages and improving efficiency
- Summary
- Abstract
- Description
- Claims
- Application Information
AI Technical Summary
Problems solved by technology
Method used
Image
Examples
Embodiment 1
[0073] First, use the existing 10 sets of fault data and 5 sets of normal data for normalization processing and training. The training data are shown in Table 1, Table 2, and Table 3.
[0074] Secondly, measure the Mahalanobis distance between 1000 sets of normalized normal data and [0]17 matrix as Figure 5 , measure the normal range Mahalanobis distance threshold n=1.9130, n1.9130 is faulty data. Through Mahalanobis distance calculation, a large number of normal data can be excluded, and only a small amount of fault data can be classified.
[0075] Then, the 6 groups of data to be tested are normalized as shown in Table 4, and the affinity is used for fault classification and judgment, including two groups of fault 1 data, two groups of fault 2 data, and two groups of normal data. The judgment results are as follows: Image 6 .
[0076] According to the failure antibody affinity as Figure 7 , the affinity is in the range of [0,0.4] and [0.6,0.7], the fault points are obv...
PUM
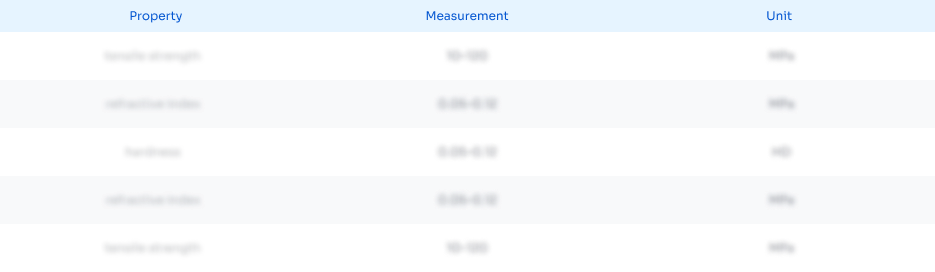
Abstract
Description
Claims
Application Information

- R&D
- Intellectual Property
- Life Sciences
- Materials
- Tech Scout
- Unparalleled Data Quality
- Higher Quality Content
- 60% Fewer Hallucinations
Browse by: Latest US Patents, China's latest patents, Technical Efficacy Thesaurus, Application Domain, Technology Topic, Popular Technical Reports.
© 2025 PatSnap. All rights reserved.Legal|Privacy policy|Modern Slavery Act Transparency Statement|Sitemap|About US| Contact US: help@patsnap.com