Three-dimensional bent-pipe multi-camera visual inspection method and system thereof
A multi-camera vision and detection method technology, applied in image data processing, instruments, calculations, etc., can solve the problems of complex operation and low measurement efficiency, and achieve the effect of easy operation and rapid detection
- Summary
- Abstract
- Description
- Claims
- Application Information
AI Technical Summary
Problems solved by technology
Method used
Image
Examples
Embodiment Construction
[0024] The present invention will be further described in detail below in conjunction with the accompanying drawings.
[0025] The present invention proposes a multi-camera visual inspection method for three-dimensional bent pipes. The basic measurement process is as follows: figure 1 shown. Taking ten-camera measurement as an example, when performing three-dimensional visual inspection of bent pipes:
[0026] Step S1, multi-camera calibration: arrange multiple marker points in the measurement field of view, and perform global calibration on the internal parameters and external parameters of multiple cameras. The marker points include circular coded marker points and circular non-coded marker points .
[0027] Taking the ten-camera measurement as an example, the global calibration of the internal and external parameters of the 10 cameras is realized by arranging multiple marker points in the measurement field of view. The layout of the 10 cameras is as follows: figure 2 sh...
PUM
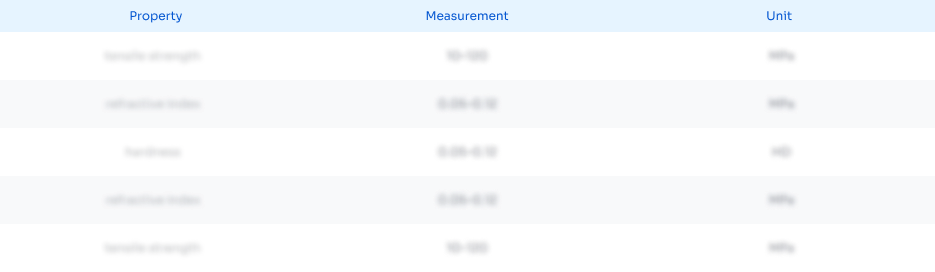
Abstract
Description
Claims
Application Information

- R&D Engineer
- R&D Manager
- IP Professional
- Industry Leading Data Capabilities
- Powerful AI technology
- Patent DNA Extraction
Browse by: Latest US Patents, China's latest patents, Technical Efficacy Thesaurus, Application Domain, Technology Topic, Popular Technical Reports.
© 2024 PatSnap. All rights reserved.Legal|Privacy policy|Modern Slavery Act Transparency Statement|Sitemap|About US| Contact US: help@patsnap.com