Aircraft rear body dynamic load follow-up loading testing device
A dynamic load and follow-up loading technology, which is applied in vibration testing, measuring devices, testing of machines/structural components, etc., can solve problems that have not been done before, and achieve stable performance, reliable work, and compact structure.
- Summary
- Abstract
- Description
- Claims
- Application Information
AI Technical Summary
Problems solved by technology
Method used
Image
Examples
Embodiment Construction
[0011] Below by embodiment the present invention will be further described:
[0012] Please also see figure 1 and figure 2 ,in, figure 1 It is a side view of the aircraft rear fuselage dynamic load follow-up loading test device of the present invention, figure 2 It is the front view of the aircraft rear fuselage dynamic load follow-up loading test device of the present invention. The aircraft rear fuselage dynamic load follow-up loading test device of the present invention comprises a vibration table 1, a movable frame 3, a support block 4, a hydraulic cylinder 6, a support seat 9, a base 10, a vertical guide rail 12, a ball head excitation rod 13, Displacement sensor 15. Wherein, the vibrating table 1 is connected with the movable frame 3 through the rotating shafts 2 at both ends. There are support blocks 4 on both sides outside the movable frame 3, the bottom of which is connected with the cylinder piston rod flange 5, and the rotating shafts 8 on both sides of the u...
PUM
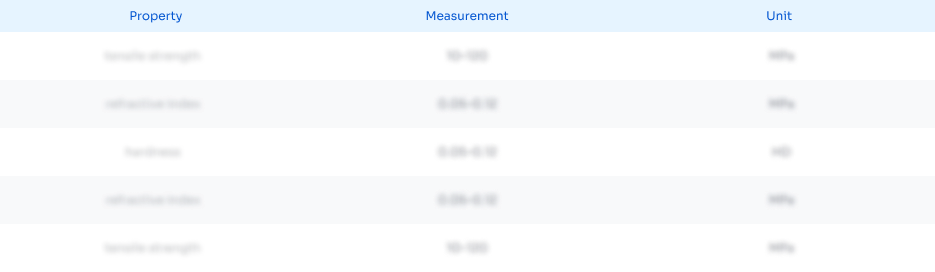
Abstract
Description
Claims
Application Information

- Generate Ideas
- Intellectual Property
- Life Sciences
- Materials
- Tech Scout
- Unparalleled Data Quality
- Higher Quality Content
- 60% Fewer Hallucinations
Browse by: Latest US Patents, China's latest patents, Technical Efficacy Thesaurus, Application Domain, Technology Topic, Popular Technical Reports.
© 2025 PatSnap. All rights reserved.Legal|Privacy policy|Modern Slavery Act Transparency Statement|Sitemap|About US| Contact US: help@patsnap.com