Segmented precise control type heat treatment process of hot-galvanized strip steels and alloying furnace thereof
An alloying furnace and hot-dip galvanizing technology, applied in heat treatment furnaces, hot dip plating processes, heat treatment equipment, etc., can solve problems such as abnormal temperature control of heat preservation, difficulty in accurate control of heat energy release, and uncertainty of heat preservation effect. , to reduce heat dissipation, protect subsequent equipment, and stabilize temperature and pressure
- Summary
- Abstract
- Description
- Claims
- Application Information
AI Technical Summary
Problems solved by technology
Method used
Image
Examples
Embodiment Construction
[0027] The present invention will be further described in detail below in conjunction with the accompanying drawings and specific embodiments.
[0028] Such as figure 1 As shown, the hot-dip galvanized steel strip subsection precise control type alloying furnace of the present invention is installed between the zinc pot 13 and the furnace top roll 12 on the galvanizing production line, and the strip steel 10 passes from the sinking roll 14 in the zinc pot 13 Lead out, through the air knife 15 to control the thickness of the galvanized layer, enter the alloying furnace for heat treatment, and finally output around the furnace top roller 12.
[0029] Such as figure 2 As shown, the alloying furnace is mainly composed of a bottom heating section 1, a middle heat preservation section 2 and an upper cooling section 3. Wherein, an induction heater 9 is arranged in the bottom heating section 1 for rapidly heating the steel strip 10 to a design temperature. The middle heat preservati...
PUM
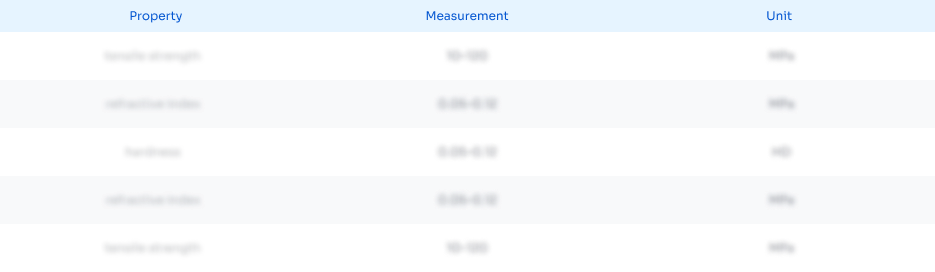
Abstract
Description
Claims
Application Information

- R&D Engineer
- R&D Manager
- IP Professional
- Industry Leading Data Capabilities
- Powerful AI technology
- Patent DNA Extraction
Browse by: Latest US Patents, China's latest patents, Technical Efficacy Thesaurus, Application Domain, Technology Topic, Popular Technical Reports.
© 2024 PatSnap. All rights reserved.Legal|Privacy policy|Modern Slavery Act Transparency Statement|Sitemap|About US| Contact US: help@patsnap.com