A Vector Propulsion Mechanism for Underwater Robot
An underwater robot and vector propulsion technology, applied in manipulators, program-controlled manipulators, manufacturing tools, etc., can solve problems such as complex structure and control, large weight-to-load ratio, and difficulty in application
- Summary
- Abstract
- Description
- Claims
- Application Information
AI Technical Summary
Problems solved by technology
Method used
Image
Examples
Embodiment Construction
[0009] The structure of the embodiment of the present invention is as figure 1 As shown, the disc base 2 is used as the static platform, and the arc-shaped slider 10 is used as the dynamic platform. There are 4 sets of motion branch chains between the dynamic and static platforms, which are respectively two sets of RP C Branch 7, 12 and two sets of RP C RU branch chain 5, 11, where RP C Branched 12 and RP C The RU branch chain 5 is an active branch chain, the ends of which are respectively connected to the servo motors 13 and 3, and the other two sets of motion branch chains, namely RP C branched chain 7 and RP C The RU branch chain 11 is a passive branch chain, which plays the role of increasing rigidity and reducing unbalanced force. The four groups of motion branch chains all include a curved moving pair P with an arc-shaped groove sliding structure C , the four sets of kinematic branch chains are located on the same spherical surface and are installed at intervals of ...
PUM
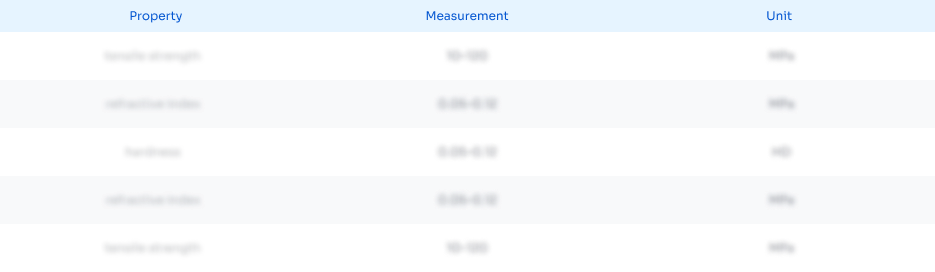
Abstract
Description
Claims
Application Information

- R&D Engineer
- R&D Manager
- IP Professional
- Industry Leading Data Capabilities
- Powerful AI technology
- Patent DNA Extraction
Browse by: Latest US Patents, China's latest patents, Technical Efficacy Thesaurus, Application Domain, Technology Topic, Popular Technical Reports.
© 2024 PatSnap. All rights reserved.Legal|Privacy policy|Modern Slavery Act Transparency Statement|Sitemap|About US| Contact US: help@patsnap.com