Brake control system of multi-wheel-train brake machine wheel
A brake control and multi-wheel train technology, applied in the field of brake systems, can solve the problems of heavy system weight, non-wireless brake control, difficult installation, etc., achieve system weight and cost reduction, prevent aircraft brake deviation, and reduce the number of components Effect
- Summary
- Abstract
- Description
- Claims
- Application Information
AI Technical Summary
Problems solved by technology
Method used
Image
Examples
Embodiment Construction
[0021] This embodiment is a brake control system for a certain four-wheeled aircraft.
[0022] The aircraft braking control system proposed in this embodiment is divided into an electrical part and a hydraulic part. Including 4 double-redundant brake command sensors 1, 2 double-redundant hydraulic cut-off valves, 4 double-redundant pressure servo valves, 4 pressure sensors 7, normal brake control unit 3, backup brake control unit 17 and 4 brakes machine wheel.
[0023] The two dual-redundancy hydraulic cut-off valves are respectively a first double-redundancy hydraulic cut-off valve 5 and a second double-redundancy hydraulic cut-off valve 15 . The four dual-redundancy pressure servo valves are respectively the first dual-redundancy pressure servo valve 6, the second double-redundancy pressure servo valve 8, the third double-redundancy pressure servo valve 13 and the fourth double-redundancy pressure servo valve 14.
[0024] The electrical part of the aircraft brake control ...
PUM
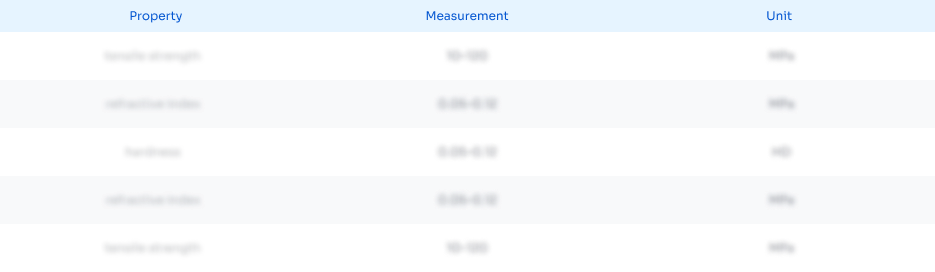
Abstract
Description
Claims
Application Information

- R&D
- Intellectual Property
- Life Sciences
- Materials
- Tech Scout
- Unparalleled Data Quality
- Higher Quality Content
- 60% Fewer Hallucinations
Browse by: Latest US Patents, China's latest patents, Technical Efficacy Thesaurus, Application Domain, Technology Topic, Popular Technical Reports.
© 2025 PatSnap. All rights reserved.Legal|Privacy policy|Modern Slavery Act Transparency Statement|Sitemap|About US| Contact US: help@patsnap.com