Drill bit and method of manufacturing machined object using same
A technology of drill bits and cutting parts, which is applied in the direction of manufacturing tools, metal processing equipment, drilling/drilling equipment, etc., which can solve the problems of material deterioration, deterioration, and drill breakage, etc., and achieve excellent breakage resistance, inhibition Effects of deflection and excellent hole machinability
- Summary
- Abstract
- Description
- Claims
- Application Information
AI Technical Summary
Problems solved by technology
Method used
Image
Examples
no. 1 approach
[0021] Below, refer to Figure 1 ~ Figure 4 , the first embodiment of the drill according to the present invention will be described in detail.
[0022] Such as figure 1 As shown in (a), the drill 1 according to this embodiment generally includes a main body (base end) 20 held by a rotating spindle of a machine tool, etc., and a cutting part 10 provided on one end side of the main body 20 . The main body portion 20 is a portion designed according to the shape of the rotating shaft of the machine tool. The cutting portion 10 is a portion in contact with the workpiece. It should be noted, figure 1 Arrow a in (a) indicates the rotation direction of the drill 1 .
[0023] The cutting portion 10 is a portion that plays a major role in cutting the workpiece. If specified, such as figure 1 (b) and figure 2 As shown in (a), the cutting part 10 of this embodiment has two cutting edges 11 (first cutting edge 11a and second cutting edge 11b ) provided at a distance from each othe...
no. 2 approach
[0050] Next, refer to Figure 5 , the drill bit according to the second embodiment of the present invention will be described in detail. It should be noted that, in Figure 5 , sometimes against the above Figure 1 ~ Figure 4 The same components are given the same reference numerals and their descriptions are omitted. It should be noted that, for the drill bit of this embodiment, figure 1 The basic structure of the drill bit 1 is the same as that of the drill bit 1 of the first embodiment, so the differences from the drill bit 1 of the first embodiment will be mainly described, and descriptions of overlapping contents will be omitted.
[0051] In this embodiment, different from the above-mentioned embodiments, as Figure 5 As shown, in the partial confluence region Y, the first groove 12a is located closer to the front end 10a side than the second groove 12b, and in the terminal region Z, only the rear end 12a3 of the first groove 12a and the second groove exist. 12b3 in ...
no. 3 approach
[0054] Next, refer to Figure 6 and Figure 7 A drill according to a third embodiment of the present invention will be described in detail. It should be noted that, in Figure 6 and Figure 7 , sometimes against the above Figure 1 to Figure 5 The same components are given the same reference numerals and their descriptions are omitted. For the drill bit of this embodiment, due to figure 1 The basic structure of the drill bit 1 is the same as that of the drill bit 1 of the first embodiment, so the differences from the drill bit 1 of the first embodiment will be mainly described, and descriptions of overlapping contents will be omitted.
[0055] In this embodiment, different from the above-mentioned embodiments, as Figure 6As shown, in the partial confluence region Y, the first groove 12a is located closer to the rear end 10b side than the second groove 12b, and in the terminal region Z, only the rear end 12a3 of the first groove 12a and the second groove 12a exist. The ...
PUM
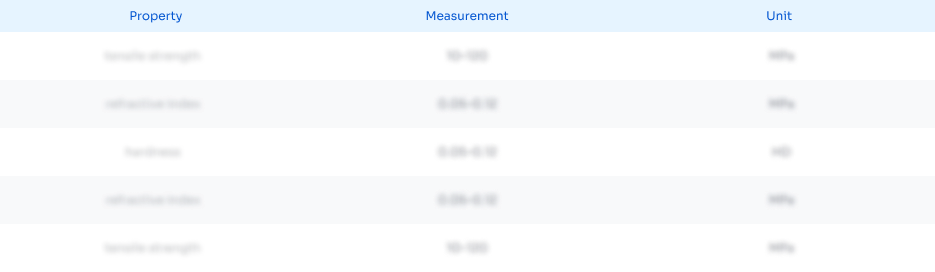
Abstract
Description
Claims
Application Information

- Generate Ideas
- Intellectual Property
- Life Sciences
- Materials
- Tech Scout
- Unparalleled Data Quality
- Higher Quality Content
- 60% Fewer Hallucinations
Browse by: Latest US Patents, China's latest patents, Technical Efficacy Thesaurus, Application Domain, Technology Topic, Popular Technical Reports.
© 2025 PatSnap. All rights reserved.Legal|Privacy policy|Modern Slavery Act Transparency Statement|Sitemap|About US| Contact US: help@patsnap.com