Oil-resistant plastic product and production method thereof
A technology for plastic products and oil resistance, applied in the field of material science, can solve the problems of poor oil resistance and dissolution, and achieve the effects of stable chemical and physical properties, simple production process and low price
- Summary
- Abstract
- Description
- Claims
- Application Information
AI Technical Summary
Problems solved by technology
Method used
Examples
Embodiment 1
[0015] (1) Take each raw material by weight: 40 parts of polyvinyl chloride, 30 parts of nitrile rubber, 42 parts of dibutyl phthalate, 0.6 part of vulcanizing agent, 0.12 parts of accelerator M, 0.6 part of accelerator DM 1.8 parts of vulcanization active agent, 0.2 parts of softener, 0.4 parts of anti-aging agent, 0.8 parts of antioxidant, 1.0 parts of barium stearate, 1.6 parts of lead stearate, 22 parts of semi-reinforcing carbon black, 3 parts of coumarone resin share;
[0016] (2) After kneading the raw materials in step (1), the temperature is 150° C., the compression ratio is 2-4, and the length-to-diameter ratio is 20-25 through twin-roll kneading, crushing, extrusion molding, cooling and setting;
[0017] (3) Cutting the cooled product processed in step (2) to obtain an oil-resistant plastic product.
[0018] Compared with the prior art, the present invention has the following advantages: (1) the plastic products produced by the present invention are cheap and the p...
Embodiment 2
[0020] (1) Take each raw material by weight: 80 parts of polyvinyl chloride, 50 parts of nitrile rubber, 62 parts of dibutyl phthalate, 1.0 parts of vulcanizing agent, 0.20 parts of accelerator M, and 1.0 parts of accelerator DM Parts, 2.2 parts of vulcanization active agent, 0.6 parts of softener, 0.6 parts of anti-aging agent, 1.2 parts of antioxidant, 1.4 parts of barium stearate, 2.0 parts of lead stearate, 42 parts of semi-reinforcing carbon black, 5 parts of coumarone resin share;
[0021] (2) After the raw materials in step (1) are kneaded, the temperature is 170° C., the compression ratio is 2-4, and the length-to-diameter ratio is 20-25, and the mixture is kneaded by twin rolls, pulverized, extruded, and cooled to shape;
[0022] (3) Cutting the cooled product processed in step (2) to obtain an oil-resistant plastic product.
[0023] Compared with the prior art, the present invention has the following advantages: (1) the plastic products produced by the present inven...
Embodiment 3
[0025] (1) Take each raw material by weight: 60 parts of polyvinyl chloride, 40 parts of nitrile rubber, 52 parts of dibutyl phthalate, 0.8 part of vulcanizing agent, 0.16 part of accelerator, 0.8 part of accelerator DM 1 part, 2 parts of vulcanization activator, 0.4 part of softener, 0.5 part of anti-aging agent, 1 part of antioxidant, 1.2 parts of barium stearate, 1.8 parts of lead stearate, 32 parts of semi-reinforcing carbon black, 4 parts of coumarone resin share;
[0026] (2) After kneading the raw materials in step (1), the temperature is 160° C., the compression ratio is 2-4, and the length-to-diameter ratio is 20-25 through twin-roll kneading, crushing, extrusion molding, cooling and setting;
[0027] (3) Cutting the cooled product processed in step (2) to obtain an oil-resistant plastic product.
[0028] Compared with the prior art, the present invention has the following advantages: (1) the plastic products produced by the present invention are cheap and the produc...
PUM
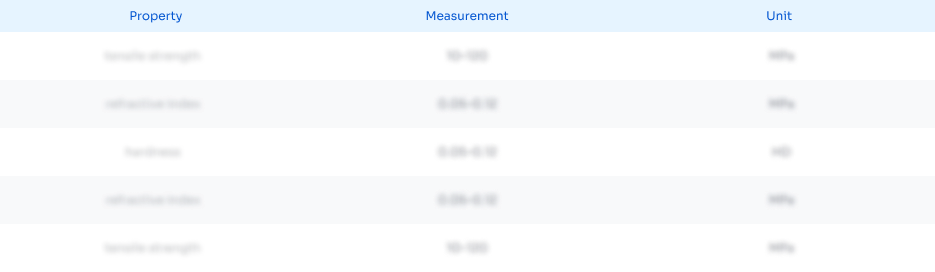
Abstract
Description
Claims
Application Information

- R&D
- Intellectual Property
- Life Sciences
- Materials
- Tech Scout
- Unparalleled Data Quality
- Higher Quality Content
- 60% Fewer Hallucinations
Browse by: Latest US Patents, China's latest patents, Technical Efficacy Thesaurus, Application Domain, Technology Topic, Popular Technical Reports.
© 2025 PatSnap. All rights reserved.Legal|Privacy policy|Modern Slavery Act Transparency Statement|Sitemap|About US| Contact US: help@patsnap.com