Tensile strained germanium MSM photoelectric detector and manufacturing method thereof
A technology for photodetectors and manufacturing methods, applied to circuits, electrical components, semiconductor devices, etc., can solve problems such as poor photoelectric detection performance, achieve the effects of improving photoelectric detection performance, reducing production costs, and enhancing tensile strain
- Summary
- Abstract
- Description
- Claims
- Application Information
AI Technical Summary
Problems solved by technology
Method used
Image
Examples
Embodiment 1
[0071] The invention provides a method for making a tensile strained germanium MSM photodetector, which at least includes the following steps:
[0072] Step S1: providing a substrate, and sequentially forming a sacrificial layer and a germanium layer on the substrate;
[0073] Step S2: forming a metal layer on the germanium layer, the metal layer providing stress to the germanium layer;
[0074] Step S3: Patterning the metal layer to form a pair of metal main bases and at least a pair of metal sub-pedestals connected to the pair of metal main bases;
[0075] Step S4: patterning the germanium layer to respectively form a germanium main pedestal and a germanium sub-pedestal under the metal main pedestal and the metal sub-pedestal, and form at least one line between each pair of germanium sub-pedestals Germanium bridge wire;
[0076] Step S5: Etching away the sacrificial layer below the germanium bridge line and the germanium sub-pedestal, so that the germanium bridge line and ...
Embodiment 2
[0093] This embodiment adopts basically the same technical solution as Embodiment 1, except that in this embodiment, metal lines connected to the metal submount are respectively formed above the two ends of the germanium bridge line.
[0094] see Figure 7 , showing a top view of the structure of the metal lines 43 connected to the metal submount 42 respectively formed above the two ends of the germanium bridge line 33 . The metal line 43 is formed synchronously with the metal main pedestal 41 and the metal sub-pedestal 42 during the patterning process of the metal layer 4 . The width of the metal line is preferably equal to the width of the germanium bridge line.
[0095] Forming metal wires 43 above the two ends of the germanium bridge wires 33 can further reduce the shear force generated on the germanium bridge wires during the film deformation process, protect the germanium bridge wires from breaking, and improve the stability of the MSM photodetector. The metal sub-pede...
Embodiment 3
[0097] This embodiment adopts basically the same scheme as Embodiment 1 or Embodiment 2. The difference is that in Embodiment 1 and Embodiment 2, uniaxial stress-strain germanium is formed, while in this embodiment, biaxial stress-strain germanium can be formed. Straining germanium can be realized only by changing the pattern of the pattern during the patterning process of the metal layer 4 and the germanium layer 3 .
[0098] Specifically, in the step S3, the metal layer is patterned to form two pairs of metal main pedestals in the horizontal and vertical directions, and a pair of metal sub-pedestals is connected between each pair of metal main pedestals; In step S4, two vertically connected germanium bridge lines are formed between the two pairs of germanium submounts; and in the step S5, after etching, the connections of the two germanium bridge lines are in both horizontal and vertical directions Stretching, forming biaxial stress and tensile strained germanium.
[0099] ...
PUM
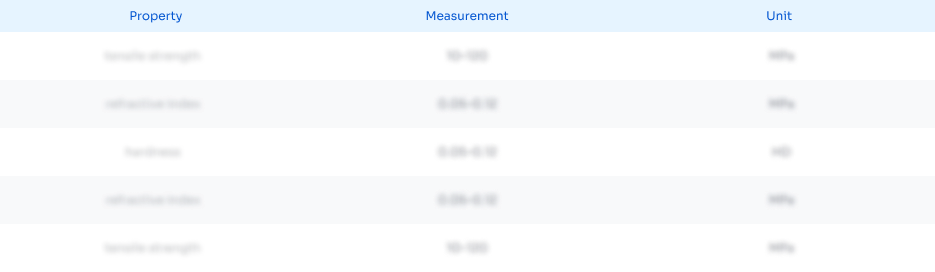
Abstract
Description
Claims
Application Information

- Generate Ideas
- Intellectual Property
- Life Sciences
- Materials
- Tech Scout
- Unparalleled Data Quality
- Higher Quality Content
- 60% Fewer Hallucinations
Browse by: Latest US Patents, China's latest patents, Technical Efficacy Thesaurus, Application Domain, Technology Topic, Popular Technical Reports.
© 2025 PatSnap. All rights reserved.Legal|Privacy policy|Modern Slavery Act Transparency Statement|Sitemap|About US| Contact US: help@patsnap.com