Method for preparing low-oxygen molybdenum and molybdenum alloy clad with Al4SiC4-HfC
A technology of al4sic4-hfc and molybdenum alloy, which is applied in the field of preparing low-oxygen metal alloys, can solve problems such as poor compatibility, shedding, coating cracking, etc., and achieve excellent hardness and wear resistance, excellent oxidation resistance, and high bonding strength Effect
- Summary
- Abstract
- Description
- Claims
- Application Information
AI Technical Summary
Problems solved by technology
Method used
Image
Examples
Embodiment 1
[0026] Will Al 4 SiC 4 Powder and HfC powder are Al by mass fraction percentage 4 SiC 4 : HfC=55% : 45% mixed evenly to get Al 4 SiC 4 -HfC powder, Al 4 SiC 4 -HfC powder and composite binder are mixed at a volume ratio of 1:3, stirred evenly, and prepared into a viscous coating filling slurry.
[0027] First, the coating filling slurry is evenly spread to the bottom of the cavity of the pressing mold, and the coating thickness of the coating filling slurry on the bottom of the cavity of the pressing mold is 1 mm. Then adopt lightweight filling block to be placed on the top of the coating, the filling block is coaxial with the cavity of the pressing mold, so that the side of the filling block and the cavity inner wall of the pressing mold enclose a semi-closed trough with a side length of 1 mm, and then Fill the trough with coating filling slurry by injection;
[0028] After the coating and filling slurry in the trough is solidified, remove the lightweight filling bloc...
Embodiment 2
[0032] Will Al 4 SiC 4 Powder and HfC powder are Al by mass fraction percentage 4 SiC 4 : HfC=60% : 40% mixed evenly to get Al 4SiC 4 -HfC powder, Al 4 SiC 4 -HfC powder and composite binder are mixed at a volume ratio of 1:3, stirred evenly, and prepared into a viscous coating filling slurry.
[0033] First, the coating filling slurry is evenly spread to the bottom of the cavity of the pressing mold, and the coating thickness of the coating filling slurry on the bottom of the cavity of the pressing mold is 2mm. Then adopt lightweight filling block to be placed on the coating top, the filling block is coaxial with the cavity of the pressing mold, so that the side of the filling block and the cavity inner wall of the pressing mold enclose a semi-closed trough with a side length of 2mm, and then Fill the trough with coating filling slurry by injection;
[0034] After the coating and filling slurry in the trough is solidified, remove the lightweight filling block; charge ...
Embodiment 3
[0037] Will Al 4 SiC 4 Powder and HfC powder are Al by mass fraction percentage 4 SiC 4 : HfC=70%: 30% mixed evenly to get Al 4 SiC 4 -HfC powder, Al 4 SiC 4 -HfC powder and composite binder are mixed at a volume ratio of 1:2, stirred evenly, and prepared into a viscous coating filling slurry.
[0038] First, the coating filling slurry is evenly spread to the bottom of the cavity of the pressing mold, and the coating thickness of the coating filling slurry on the bottom of the cavity of the pressing mold is 2mm. Then adopt lightweight filling block to be placed on the coating top, the filling block is coaxial with the cavity of the pressing mold, so that the side of the filling block and the cavity inner wall of the pressing mold enclose a semi-closed trough with a side length of 2mm, and then Fill the trough with coating filling slurry by injection.
[0039] After the coating and filling slurry in the trough is solidified, remove the lightweight filling block; charge ...
PUM
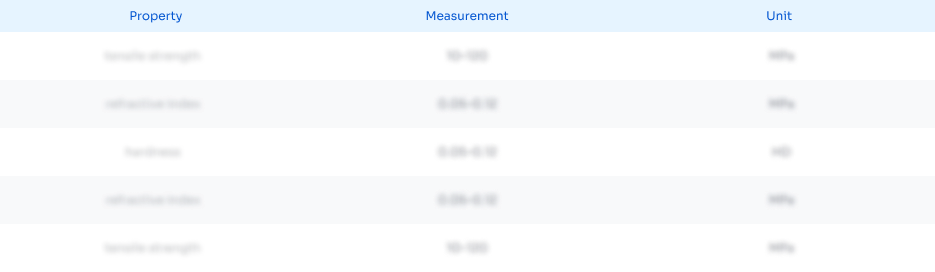
Abstract
Description
Claims
Application Information

- R&D
- Intellectual Property
- Life Sciences
- Materials
- Tech Scout
- Unparalleled Data Quality
- Higher Quality Content
- 60% Fewer Hallucinations
Browse by: Latest US Patents, China's latest patents, Technical Efficacy Thesaurus, Application Domain, Technology Topic, Popular Technical Reports.
© 2025 PatSnap. All rights reserved.Legal|Privacy policy|Modern Slavery Act Transparency Statement|Sitemap|About US| Contact US: help@patsnap.com