Industrial joint robot body
A robot body and joint technology, applied in manipulators, manufacturing tools, program-controlled manipulators, etc., can solve the problems of high component dependence, troublesome processing, complex structure, etc., achieve strong program control, easy manufacturing and installation, and avoid coupling phenomenon Effect
- Summary
- Abstract
- Description
- Claims
- Application Information
AI Technical Summary
Problems solved by technology
Method used
Image
Examples
Embodiment Construction
[0017] Below by embodiment and in conjunction with accompanying drawing, the present invention will be further described:
[0018] Such as figure 1 The shown industrial joint robot body consists of a base frame 1, a large arm 2, a small arm 3, a connecting rod 4, a first drive motor 5, a first reducer 6, a main drive connection plate 7, a large arm turntable 8, and a large arm Base bracket 9, boom shaft 10, second drive motor 11, second reducer 12, spline 13, motor mounting plate 14, third drive motor 15, third reducer 16, boom flange 17, Forearm bracket 18, forearm shaft 19, work surface 20, plane bearing 21, table support block 22, mechanical claw motor mounting flange 23, reducer mounting connection plate 24, first encoder 25, second encoder 26 , The third encoder 27, the driving synchronous pulley 28, the driven synchronous pulley 29, the mounting bracket 30, the motor support angle bracket 31 and the like.
[0019] There is a cavity inside the base frame 1 , and a first...
PUM
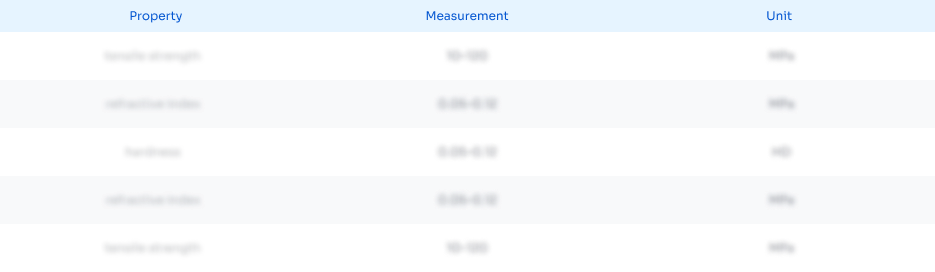
Abstract
Description
Claims
Application Information

- R&D
- Intellectual Property
- Life Sciences
- Materials
- Tech Scout
- Unparalleled Data Quality
- Higher Quality Content
- 60% Fewer Hallucinations
Browse by: Latest US Patents, China's latest patents, Technical Efficacy Thesaurus, Application Domain, Technology Topic, Popular Technical Reports.
© 2025 PatSnap. All rights reserved.Legal|Privacy policy|Modern Slavery Act Transparency Statement|Sitemap|About US| Contact US: help@patsnap.com