LED (Light-Emitting Diode) radiating fin splicing method and equipment
A heat sink and equipment technology, applied in welding equipment, heat exchange equipment, non-electric welding equipment, etc., can solve the problem that the welding method cannot meet the requirements
- Summary
- Abstract
- Description
- Claims
- Application Information
AI Technical Summary
Problems solved by technology
Method used
Image
Examples
Embodiment Construction
[0021] In order to further understand the features, technical means, specific objectives and functions achieved by the present invention, and to analyze the advantages and spirit of the present invention, a further understanding of the present invention can be obtained through the following detailed description of the present invention in conjunction with the accompanying drawings and specific embodiments.
[0022] See attached figure 1 , which is a schematic flowchart of a method for splicing LED heat sinks according to an embodiment of the present invention.
[0023] The LED heat sink splicing method includes steps:
[0024] Step S110: align and fix the LED heat sinks to be spliced, and form splicing seams between adjacent LED heat sinks to be spliced.
[0025] Since there will be external force on the LED heat sink during the welding process, it is necessary to fix the LED heat sink to avoid displacement during the welding process. The LED heat sink exerts pressure.
[0...
PUM
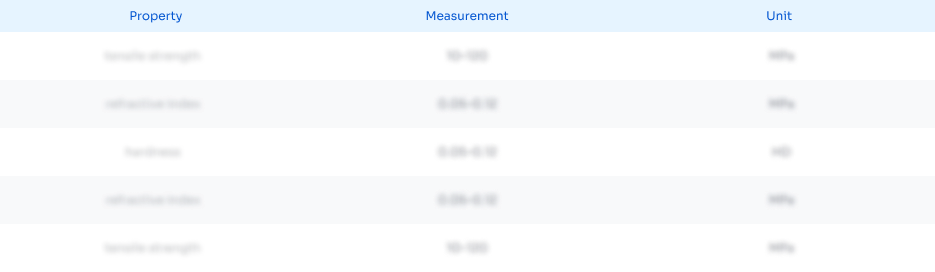
Abstract
Description
Claims
Application Information

- R&D Engineer
- R&D Manager
- IP Professional
- Industry Leading Data Capabilities
- Powerful AI technology
- Patent DNA Extraction
Browse by: Latest US Patents, China's latest patents, Technical Efficacy Thesaurus, Application Domain, Technology Topic, Popular Technical Reports.
© 2024 PatSnap. All rights reserved.Legal|Privacy policy|Modern Slavery Act Transparency Statement|Sitemap|About US| Contact US: help@patsnap.com