A film drying method applied to sol coating technology
A drying method and sol technology, applied in liquid chemical plating, metal material coating process, coating and other directions, to achieve the effect of simple operation process, no shrinkage deformation, simple and controllable process
- Summary
- Abstract
- Description
- Claims
- Application Information
AI Technical Summary
Problems solved by technology
Method used
Image
Examples
Embodiment 1
[0021] 1) Take a certain mass of vanadyl acetylacetonate and an appropriate volume of ethanol to fully mix and stir, and leave to stand for 5 hours to form a vanadium dioxide coating solution.
[0022] 2) Coating the coating solution described in step (1) on the cleaned glass substrate by spray pyrolysis method.
[0023] 3) Place the glass substrate coated with vanadium dioxide coating solution horizontally figure 1 In the middle of the heating furnace shown, the temperature is rapidly raised to 80°C at a heating rate of 5°C / s, and taken out after holding for 10 minutes to obtain a dry film with almost no shrinkage deformation.
Embodiment 2
[0025] 1) Take a certain quality of zinc acetate and an appropriate volume of ethylene glycol methyl ether, mix and stir thoroughly, and form a zinc oxide coating solution after standing for 5 hours.
[0026] 2) Coating the coating solution described in step (1) on the cleaned silicon wafer substrate by a spin coating method.
[0027] 3) Place the silicon substrate coated with zinc oxide coating solution horizontally figure 1 In the center of the heating furnace shown, the temperature is rapidly raised to 300°C at a heating rate of 10°C / s, and taken out after holding for 1 minute to obtain a dry film with almost no shrinkage deformation.
Embodiment 3
[0029] 1) Take a certain volume of tetraethyl orthosilicate, fully mix and stir with an appropriate volume of water and dilute hydrochloric acid solution, and form a silicon oxide coating solution after standing for 5 hours.
[0030] 2) Coating the coating solution described in step (1) on the cleaned quartz substrate by a pulling method.
[0031] 3) Put the quartz substrate coated with silicon oxide coating solution horizontally into figure 1 In the middle of the heating furnace shown, the temperature is rapidly raised to 200°C at a heating rate of 8°C / s, and taken out after holding for 5 minutes to obtain a dry film with almost no shrinkage deformation.
PUM
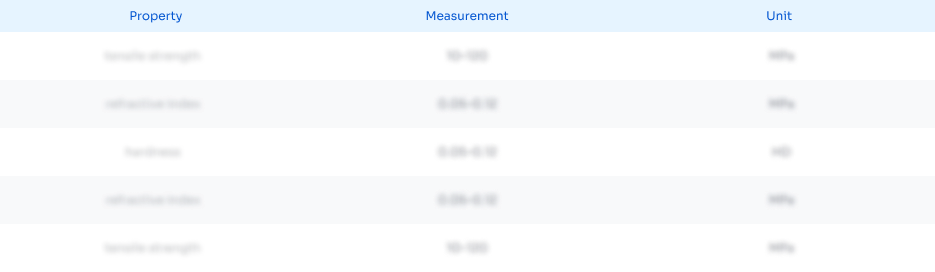
Abstract
Description
Claims
Application Information

- R&D
- Intellectual Property
- Life Sciences
- Materials
- Tech Scout
- Unparalleled Data Quality
- Higher Quality Content
- 60% Fewer Hallucinations
Browse by: Latest US Patents, China's latest patents, Technical Efficacy Thesaurus, Application Domain, Technology Topic, Popular Technical Reports.
© 2025 PatSnap. All rights reserved.Legal|Privacy policy|Modern Slavery Act Transparency Statement|Sitemap|About US| Contact US: help@patsnap.com