Biomass fuel anti-coking additive
A biomass fuel and biomass raw material technology, applied in the direction of fuel, solid fuel, petroleum industry, etc., can solve the problems of low ash melting point, low fuel utilization rate and combustion efficiency, corrosion of combustion equipment, etc., to solve coking and improve fuel efficiency. Utilization rate and combustion efficiency, effect of increasing ash melting point
- Summary
- Abstract
- Description
- Claims
- Application Information
AI Technical Summary
Problems solved by technology
Method used
Examples
Embodiment 1
[0014] Example 1: Anti-coking additives for biomass fuels such as cotton stalks and larch
[0015] Cotton straw, larch and other raw materials contain relatively low Si and other alkali metal elements. The Si content is basically below 10%, the K content is about 4%, and the coking rate after combustion is low. This anti-coking additive is mainly used for Improve the combustion characteristics of briquette fuels, so the anti-coking additives used for cotton stalks, larch and other biomass fuels are composed of 20% alumina, 15% magnesium carbonate and 65% calcium oxide uniformly mixed in a dry container. And use according to 2% of the total weight of biomass raw materials. After combustion, the ash content of the fuel was analyzed. Compared with the control group (without additives), the coking rate of the cotton straw pellet fuel dropped from 21% to 5%, and the ash melting point reached 1260°C; the coking rate of the larch straw pellet fuel decreased from 9%. Dropped to 1%, t...
Embodiment 2
[0016] Example 2: Anti-coking additives for biomass fuels such as wheat straw and rice straw
[0017] Raw materials such as wheat straw and rice straw contain generally high Si elements and other alkali metal elements. The Si content is basically about 20%, and the K element content is about 10%. The coking rate after combustion is high, so it is used for wheat straw, rice The anti-coking additive for biomass fuels such as stalks is composed of 25% alumina, 25% magnesium carbonate and 50% calcium oxide uniformly mixed in a dry container by weight percentage, and is added according to 5% of the total weight of biomass raw materials. After combustion, the ash content of the fuel was analyzed. Compared with the control group (without additives), the coking rate of the wheat straw pellet fuel dropped from 32% to 11%, and the ash melting point reached 1290°C; the coking rate of the larch straw pellet fuel decreased from 22% Dropped to 3%, the ash melting point reached 1340°C. Comb...
Embodiment 3
[0018] Example 3: Anti-coking additives for biomass fuels such as corn stalks and Korean pine
[0019] Corn stalks, Korean pine and other raw materials contain relatively high Si elements and other alkali metal elements. The Si content is basically about 25%, the K element content is about 15%, and the coking rate after combustion is the highest. The anti-coking additive for biomass fuel is composed of 30% aluminum oxide, 30% magnesium carbonate and 40% calcium oxide uniformly mixed in a dry container by weight percentage, and added according to 8% of the total weight of biomass raw materials. After combustion, the ash content of the fuel was analyzed. Compared with the control group (without additives), the coking rate of the corn stalk pellet fuel decreased from 47% to 14%, and the ash melting point reached 1380°C; the coking rate of the Korean pine pellet fuel decreased from 53%. To 17%, the ash melting point reaches 1540°C. Combustion efficiency increased by about 6%.
...
PUM
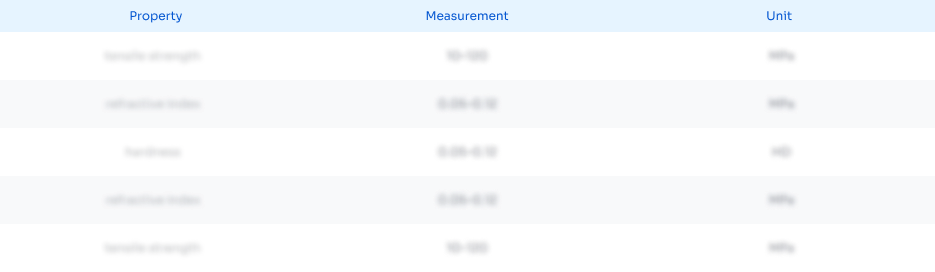
Abstract
Description
Claims
Application Information

- R&D
- Intellectual Property
- Life Sciences
- Materials
- Tech Scout
- Unparalleled Data Quality
- Higher Quality Content
- 60% Fewer Hallucinations
Browse by: Latest US Patents, China's latest patents, Technical Efficacy Thesaurus, Application Domain, Technology Topic, Popular Technical Reports.
© 2025 PatSnap. All rights reserved.Legal|Privacy policy|Modern Slavery Act Transparency Statement|Sitemap|About US| Contact US: help@patsnap.com