MnZn ferrite material of low loss and high saturation magnetic flux density and preparation method of MnZn ferrite material
A technology of ferrite material and magnetic flux density, applied in the field of MnZn ferrite material and its preparation, low loss and high saturation magnetic flux density MnZn ferrite material and its preparation field, can solve problems such as NiO addition research, achieve Increased saturation magnetic flux density, improved low loss, and reasonable design effects
- Summary
- Abstract
- Description
- Claims
- Application Information
AI Technical Summary
Problems solved by technology
Method used
Examples
Embodiment 1
[0019] will consist of 54.0mol% Fe 2 O 3 , 6.0 mol% ZnO, 36.0 mol% MnO and 4.0 mol% NiO were mixed in a sand mill for 1 hour, and then pre-fired at 850 °C for 2 hours. Based on the quality of the powder after pre-sintering, add auxiliary components to the above-mentioned pre-sintering materials, and the auxiliary components added are: 150ppm SiO 2 , 1000ppm CaCO 3 , 400ppm Nb 2 O 5 , 1000ppm SnO 2 , 200ppm ZrO 2 and 800ppm Co 2 O 3 . Then carry out secondary sand grinding for 2 hours, add PVA, spray granulation, and shape into a standard ring magnetic core of Φ25 for sintering. Incubate at 1300°C for 5 hours, maintaining the partial pressure of oxygen at 10%.
[0020] Use the CH2335 loss tester to test the loss of the sample at 100kHz, 200mT, 100℃, and the result is 315kW / m 3 , with SY-8219 type B-H tester at 50Hz, 1200A / m, 100°C to test the Bs of the sample, the result is 471mT.
Embodiment 2
[0024] will consist of 54.5mol% Fe 2 O 3 , 6.5 mol % ZnO, 36.2 mol % MnO and 2.8 mol % NiO were mixed in a sand mill for 1 hour, and then pre-fired at 850 °C for 2 hours. Based on the quality of the powder after pre-sintering, add auxiliary components to the above-mentioned pre-sintering materials, and the auxiliary components added are: 150ppm SiO 2 , 800ppm CaCO 3 , 300ppm Nb 2 O 5 , 800ppm SnO 2 , 300ppm ZrO 2 and 700ppm Co 2 O 3 . Then carry out secondary sand grinding for 2 hours, add PVA, spray granulation, and shape into a standard ring magnetic core of Φ25 for sintering. Incubate at 1300°C for 5 hours, maintaining the partial pressure of oxygen at 10%.
[0025] Use the CH2335 loss tester to test the loss of the sample at 100kHz, 200mT, 100℃, and the result is 298kW / m 3 , with the SY-8219 B-H tester at 50Hz, 1200A / m, 100 ℃ to test the Bs of the sample, the result is 475mT.
Embodiment 3
[0029] will consist of 55mol% Fe 2 O 3 , 6.3 mol % ZnO, 36.5 mol % MnO and 2.2 mol % NiO were mixed in a sand mill for 1 hour, and then pre-fired at 850 °C for 2 hours. Based on the quality of the powder after pre-sintering, add auxiliary components to the above-mentioned pre-sintering materials, and the auxiliary components added are: 200ppm SiO 2 , 800ppm CaCO 3 , 250ppm Nb 2 O 5 , 800ppm SnO 2 , 200ppm ZrO 2 and 900ppm Co 2 O 3 . Then carry out secondary sand grinding for 2 hours, add PVA, spray granulation, and shape into a standard ring magnetic core of Φ25 for sintering. Incubate at 1300°C for 5 hours, maintaining the partial pressure of oxygen at 10%.
[0030] Using the CH2335 loss tester to test the loss of the sample at 100kHz, 200mT, 100℃, the result is 281kW / m 3 , with SY-8219 type B-H tester at 50Hz, 1200A / m, 100℃ to test the Bs of the sample, the result is 478mT.
PUM
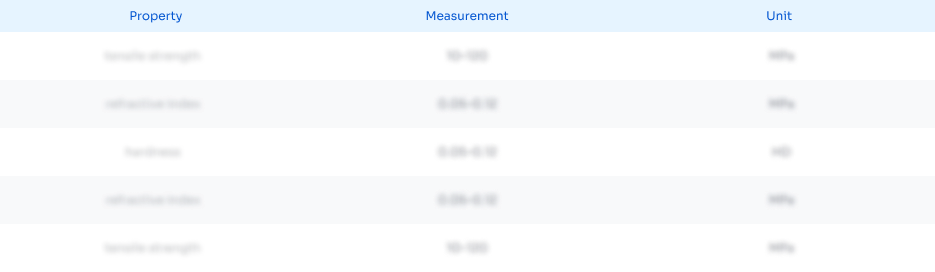
Abstract
Description
Claims
Application Information

- R&D Engineer
- R&D Manager
- IP Professional
- Industry Leading Data Capabilities
- Powerful AI technology
- Patent DNA Extraction
Browse by: Latest US Patents, China's latest patents, Technical Efficacy Thesaurus, Application Domain, Technology Topic, Popular Technical Reports.
© 2024 PatSnap. All rights reserved.Legal|Privacy policy|Modern Slavery Act Transparency Statement|Sitemap|About US| Contact US: help@patsnap.com