Method for preparing foam cement by utilizing fly ash ceramsite as lightweight aggregate
A technology of fly ash ceramsite and foamed cement, which is applied in the field of building materials, can solve the problems of ceramsite floating, low thermal conductivity, unreasonable utilization of cultivated land resources, etc., to improve bonding strength, mechanical properties and durability, Solve the effect of ceramsite floating
- Summary
- Abstract
- Description
- Claims
- Application Information
AI Technical Summary
Problems solved by technology
Method used
Image
Examples
Embodiment 1
[0026] Step a11, adding 0.5 g of sodium carboxymethyl cellulose to 110 mL of water, and standing still to fully dissolve the sodium carboxymethyl cellulose into the water to obtain an aqueous solution of sodium carboxymethyl cellulose;
[0027] Step b11, add 1.2g of 10% polyvinyl alcohol solution to the above solution, stir evenly, then, while stirring, add 100g of fly ash ceramsite and a mixture successively, the mixture includes 240g of cement, two Manganese oxide 0.2g, naphthalene-based water reducer 0.3g, stir evenly, finally, add 15mL hydrogen peroxide with a concentration of 30% to the uniformly mixed slurry, stir rapidly for 15s, put into the mold, harden and form, and finally set after 1 day, Remove the mold, spray water indoors or cover with a film to keep it moist for 28 days to the test age, and then get the fly ash ceramsite foamed cement.
[0028] Wherein, in the described step b12, the mass ratio of polyvinyl alcohol solution (10%) and carboxymethyl cellulose in ...
Embodiment 2
[0030] Step a21, adding 0.5 g of sodium carboxymethyl cellulose into 115 mL of water, and standing still to fully dissolve the sodium carboxymethyl cellulose into the water to obtain an aqueous solution of sodium carboxymethyl cellulose;
[0031] Step b21, add 1.3g of 10% polyvinyl alcohol solution to the above solution, stir evenly, then, while stirring, add 100g of fly ash ceramsite and mixture successively, the mixture includes 240g of cement, two Manganese oxide 0.2g, naphthalene-based water reducer 0.3g, stir evenly, finally, add 15mL hydrogen peroxide with a concentration of 30% to the uniformly mixed slurry, stir rapidly for 15s, put into the mold, harden and form, and finally set after 1 day, Remove the mold, spray water indoors or cover it with a film for 28 days to the test age, and then get the fly ash ceramsite foamed cement.
[0032] Wherein, the mass ratio of the 10% polyvinyl alcohol solution in the described step b21 to the sodium carboxymethyl cellulose in the...
Embodiment 3
[0034] In step a31, add 0.5 g of sodium carboxymethyl cellulose to 105 mL of water, and let the sodium carboxymethyl cellulose fully dissolve in the water to obtain an aqueous solution of sodium carboxymethyl cellulose;
[0035] Step b31, add 1.4g of 10% polyvinyl alcohol solution to the above solution, stir evenly, and then, while stirring, add 100g of shale ceramsite and mixture successively, the mixture includes 220g of cement, carbon dioxide Manganese 0.2g, naphthalene-based water reducer 0.3g, stir evenly, finally, add 15mL hydrogen peroxide with a concentration of 30% to the uniformly mixed slurry, stir rapidly for 15s, put into the mold, harden and form, final set after 1 day, remove Moisturizing and spraying water indoors or covering with film for curing for 28 days to the test age to obtain shale ceramsite foamed cement.
[0036] Wherein, the mass ratio of the 10% polyvinyl alcohol solution in the step b31 to the sodium carboxymethyl cellulose in the sodium carboxymet...
PUM
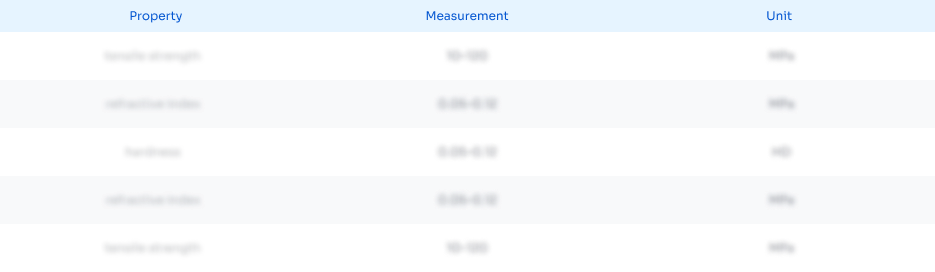
Abstract
Description
Claims
Application Information

- R&D Engineer
- R&D Manager
- IP Professional
- Industry Leading Data Capabilities
- Powerful AI technology
- Patent DNA Extraction
Browse by: Latest US Patents, China's latest patents, Technical Efficacy Thesaurus, Application Domain, Technology Topic, Popular Technical Reports.
© 2024 PatSnap. All rights reserved.Legal|Privacy policy|Modern Slavery Act Transparency Statement|Sitemap|About US| Contact US: help@patsnap.com