Composite metal wire and manufacturing method
A metal composite, wire technology, applied in the direction of metal/alloy conductors, cable/conductor manufacturing, conductors, etc., can solve the problems of hard material, high elasticity, high processing cost, and achieve the effect of low loss
- Summary
- Abstract
- Description
- Claims
- Application Information
AI Technical Summary
Problems solved by technology
Method used
Examples
Embodiment Construction
[0017] A metal composite wire, which is composed of a core body and a cladding layer, wherein the cladding layer is copper, especially copper with a weight purity of 99.90-99.98%; the core body is made of 35% copper by weight, 55% iron by weight and aluminum 10% iron alloy by weight; the thickness of the cladding layer is 1 / 4-1 / 2 of the wire radius.
[0018] The wire blank is drawn by a wire drawing machine through a multi-pass drawing die, so that the interface of copper and iron alloy is metallurgically combined to form a wire with a required wire diameter.
[0019] Its preparation method comprises the following steps:
[0020] Remove the grease and oxidation passivation layer on the surface of copper strip and ferroalloy wire;
[0021] Copper is coated on the iron alloy wire with a diameter of 10mm-12mm to make a composite billet;
[0022] Draw the composite blank to a diameter of 3-5mm at a speed of 120m / min-150m / min and a diameter reduction rate of 13-18%;
[0023] Adj...
PUM
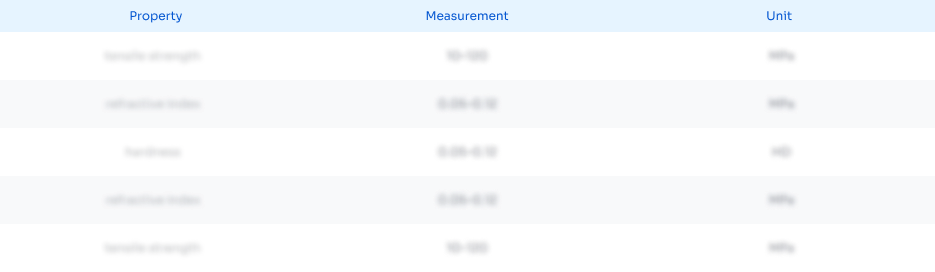
Abstract
Description
Claims
Application Information

- R&D Engineer
- R&D Manager
- IP Professional
- Industry Leading Data Capabilities
- Powerful AI technology
- Patent DNA Extraction
Browse by: Latest US Patents, China's latest patents, Technical Efficacy Thesaurus, Application Domain, Technology Topic, Popular Technical Reports.
© 2024 PatSnap. All rights reserved.Legal|Privacy policy|Modern Slavery Act Transparency Statement|Sitemap|About US| Contact US: help@patsnap.com