Integrated system and method used for preparing aromatic hydrocarbons from methyl alcohol
A technology for aromatics and methanol, which is applied in the field of integrated systems for producing aromatics, can solve the problems of high energy consumption, complex process flow, and failure to realize the reuse of heavy aromatics, so as to reduce coking rate, save investment and energy consumption, and prolong service life cycle effect
- Summary
- Abstract
- Description
- Claims
- Application Information
AI Technical Summary
Problems solved by technology
Method used
Image
Examples
Embodiment 1
[0036] The methanol aromatization reactor adopts a fixed bed reactor, and the controlled reaction conditions are: temperature 360°C, pressure 2.0MPa, methanol WHSV=1.0h -1 , Circulation gas: methanol = 6 (molar ratio), the catalyst uses Ga / Zn-ZSM-5 molecular sieve catalyst, based on the catalyst, the Ga content is 1.0%, and the Zn content is 0.5%. The liquefied gas aromatization reactor adopts a fixed-bed reactor, and the controlled reaction conditions are: temperature 450°C, pressure 0.5MPa, raw material WHSV=1.0h -1 , the catalyst uses Ga / Ce-ZSM-5 molecular sieve catalyst, based on the catalyst, the Ga content is 1.5%, and the Ce content is 0.5%. The transalkylation reactor adopts a fixed bed reactor, and the controlled reaction conditions are: temperature 220°C, pressure 1.2MPa, raw material WHSV=1.0h -1 , the catalyst is Mo / Ni-Y molecular sieve catalyst, based on the catalyst, the Mo content is 1.5%, and the Ni content is 1.0%. Under the above process conditions, the yie...
Embodiment 2
[0038] The methanol aromatization reactor adopts a moving bed reactor, and the controlled reaction conditions are: temperature 420°C, pressure 0.2MPa, methanol WHSV=1.5h -1 , Circulation gas: methanol = 3 (molar ratio), the catalyst uses Ga / Ni-ZSM-5 molecular sieve catalyst, based on the catalyst, the Ga content is 2.0%, and the Ni content is 1.0%. The liquefied gas aromatization reactor adopts a moving bed reactor, and the controlled reaction conditions are: temperature 500°C, pressure 0.2MPa, raw material WHSV=0.8h -1 , the catalyst uses Ga / Fe-ZSM-5 molecular sieve catalyst, based on the catalyst, the Ga content is 3.0%, and the Fe content is 2.0%. The transalkylation reactor adopts a fixed bed reactor, and the controlled reaction conditions are: temperature 300°C, pressure 1.8MPa, raw material WHSV=0.7h -1 , the catalyst adopts Mo / La-Y molecular sieve catalyst, based on the catalyst, the Mo content is 3.0%, and the La content is 0.3%. Under the above process conditions, t...
Embodiment 3
[0040] The methanol aromatization reactor adopts a fluidized bed reactor, and the controlled reaction conditions are: temperature 480°C, pressure 0.2MPa, methanol WHSV=2.0h -1 , the catalyst adopts Ga / La-ZSM-5 molecular sieve catalyst, based on the catalyst, the Ga content is 3.0%, and the La content is 1.0%. The liquefied gas aromatization reactor adopts a fluidized bed reactor, and the controlled reaction conditions are: temperature 550°C, pressure 0.2MPa, raw material WHSV=1.5h -1 , the catalyst adopts Ga / Zn-ZSM-5 molecular sieve catalyst, based on the catalyst, the Ga content is 3.0%, and the Zn content is 1.0%. The transalkylation reactor adopts a fixed bed reactor, and the controlled reaction conditions are: temperature 350°C, pressure 2.0MPa, raw material WHSV=1.2h -1 , the catalyst uses Mo / Co-Y molecular sieve catalyst, based on the catalyst, the Mo content is 3.0%, and the Co content is 2.0%. Under the above process conditions, the yields of each product are shown i...
PUM
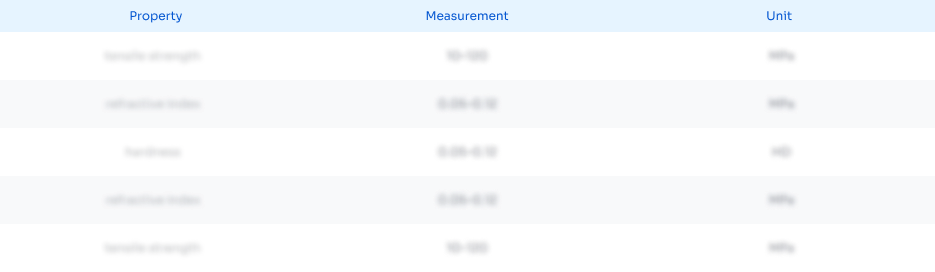
Abstract
Description
Claims
Application Information

- R&D Engineer
- R&D Manager
- IP Professional
- Industry Leading Data Capabilities
- Powerful AI technology
- Patent DNA Extraction
Browse by: Latest US Patents, China's latest patents, Technical Efficacy Thesaurus, Application Domain, Technology Topic, Popular Technical Reports.
© 2024 PatSnap. All rights reserved.Legal|Privacy policy|Modern Slavery Act Transparency Statement|Sitemap|About US| Contact US: help@patsnap.com