Forming method of precise high-temperature alloy pipe with small caliber and thick wall for aviation
A high-temperature alloy and forming method technology, which is applied in the field of forming small-diameter thick-walled high-temperature alloy tubes, can solve the problems of restricting the research and development and production of aero-engines, high manufacturing difficulty, and high price, so as to reduce the loss of main materials and save costs , Guarantee the effect of quality
- Summary
- Abstract
- Description
- Claims
- Application Information
AI Technical Summary
Problems solved by technology
Method used
Examples
Embodiment 1
[0031] To manufacture a finished tube with an outer diameter of 8.5mm, a wall thickness of 2.7mm, and a length of 4m, the steps are as follows:
[0032] First of all, adopt LG-30, LD-30, LD-15 and other cold rolling mills to carry out multi-pass cold rolling on the qualified seamless tube billet to obtain a tube billet with an excessive specification. The outer diameter of the tube blank with the transitional specification is 9.9 mm, the wall thickness is 2.6mm, the length is 3300mm, and the dimensional deviation of the outer diameter and wall thickness is controlled within ±0.03mm.
[0033] Then, carry out degreasing, heat treatment, pickling, straightening, and UT flaw detection on transitional specification tube blanks according to the above method, select qualified tube blanks obtained through UT flaw detection, and point them. Finished tube.
Embodiment 2
[0035] To manufacture a finished tube with an outer diameter of 8.3mm, a wall thickness of 2.5mm, and a length of 3.5m, the steps are as follows:
[0036] First of all, adopt LG-30, LD-30, LD-15 and other cold rolling mills to carry out multi-pass cold rolling on the qualified seamless tube billet to obtain a tube billet with an excessive specification. The outer diameter of the tube blank with the transitional specification is 9.5 mm, the wall thickness is 2.45mm, the length is 2950mm, and the dimensional deviation of the outer diameter and wall thickness is controlled within ±0.03mm.
[0037] Then, carry out degreasing, heat treatment, pickling, straightening, and UT flaw detection on transitional specification tube blanks according to the above method, select qualified tube blanks obtained through UT flaw detection, and point them. Finished tube.
Embodiment 3
[0039] To manufacture a finished tube with a diameter of 8mm, a wall thickness of 2.3mm, and a length of 3m, the steps are as follows:
[0040] First of all, adopt LG-30, LD-30, LD-15 and other cold rolling mills to carry out multi-pass cold rolling on the qualified seamless tube billet to obtain a tube billet with an excessive specification. The outer diameter of the tube blank with the transitional specification is 9.15 mm, the wall thickness is 2.25mm, the length is 2550mm, and the dimensional deviation of the outer diameter and wall thickness is controlled within ±0.03mm.
[0041] Then, carry out degreasing, heat treatment, pickling, straightening, and UT flaw detection on transitional specification tube blanks according to the above method, select qualified tube blanks obtained through UT flaw detection, and point them. Finished tube.
[0042] After inspection, the quality and precision of the finished tubes produced by the above three implementation methods all meet the...
PUM
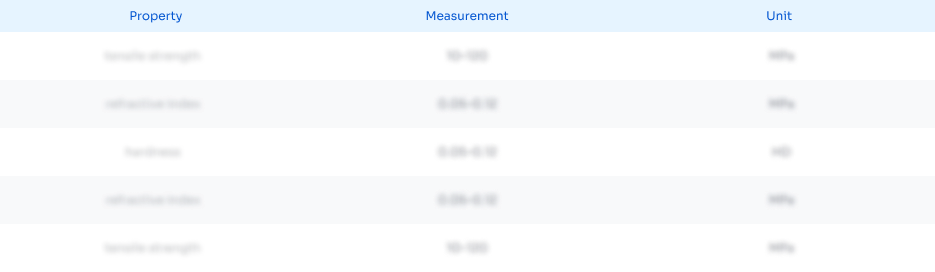
Abstract
Description
Claims
Application Information

- Generate Ideas
- Intellectual Property
- Life Sciences
- Materials
- Tech Scout
- Unparalleled Data Quality
- Higher Quality Content
- 60% Fewer Hallucinations
Browse by: Latest US Patents, China's latest patents, Technical Efficacy Thesaurus, Application Domain, Technology Topic, Popular Technical Reports.
© 2025 PatSnap. All rights reserved.Legal|Privacy policy|Modern Slavery Act Transparency Statement|Sitemap|About US| Contact US: help@patsnap.com