M-phase permanent magnet motor control method for directly solving pulse width modulation through duty ratios
A pulse width modulation, permanent magnet motor technology, used in motor generator control, AC motor control, electronic commutation motor control, etc. The effect of simplifying complexity
- Summary
- Abstract
- Description
- Claims
- Application Information
AI Technical Summary
Problems solved by technology
Method used
Image
Examples
Embodiment 1
[0033] Embodiment 1: as figure 1 As shown, when the windings of the M-phase permanent magnet motor are sinusoidally distributed, the duty ratio is used to directly solve the M-phase permanent magnet motor control method of pulse width modulation, through the photoelectric encoder 5, including a speed outer ring and M-1 current The vector control module 6 of the inner loop, the duty ratio direct solution pulse width modulation module 7 and the M-phase voltage type inverter 3 control the M-phase permanent magnet motor 4, including the following specific steps:
[0034] Step 1), in each control cycle, the motor rotor position θ is measured and calculated by the photoelectric encoder 5 r and the actual rotor speed ω r ;
[0035] Step 2), the given speed value of the motor and actual speed ω r After comparison, the quadrature-axis current component of the fundamental wave of the given electromagnetic torque is obtained through the PI regulator of the outer ring of the speed ...
Embodiment 2
[0065] Embodiment 2: When the windings of the M-phase permanent magnet motor are distributed at a concentrated and full distance, the control method of the M-phase permanent magnet motor that directly solves the pulse width modulation by using the duty ratio is based on the sinusoidal power supply, and only needs to combine the harmonic injection rate The motor smoothly transitions from a sinusoidal power supply state to a non-sinusoidal power supply state, while the output torque increases.
PUM
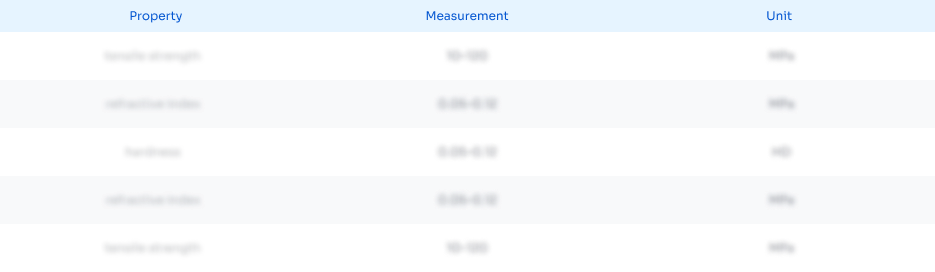
Abstract
Description
Claims
Application Information

- R&D Engineer
- R&D Manager
- IP Professional
- Industry Leading Data Capabilities
- Powerful AI technology
- Patent DNA Extraction
Browse by: Latest US Patents, China's latest patents, Technical Efficacy Thesaurus, Application Domain, Technology Topic, Popular Technical Reports.
© 2024 PatSnap. All rights reserved.Legal|Privacy policy|Modern Slavery Act Transparency Statement|Sitemap|About US| Contact US: help@patsnap.com