Fin and wing aeroelasticity test device of high-speed wind tunnel
An aeroelastic, high-speed wind tunnel technology, applied in the direction of aerodynamic testing, measuring devices, testing of machine/structural components, etc., can solve the problem of insertion mechanism support stiffness affecting structural dynamic characteristics, difficult model system joint control test protection automation , slow response speed and other issues, to achieve the effect of compact structure, small flow field blockage and large load
- Summary
- Abstract
- Description
- Claims
- Application Information
AI Technical Summary
Problems solved by technology
Method used
Image
Examples
Embodiment Construction
[0026] figure 1 It is a schematic diagram of the aeroelastic test device for rudder airfoil in a high-speed wind tunnel. In the figure 1 is a model (rudder surface model or airfoil model), 2 is a "V" protective cover, 3 is a reflector, 4 is a support baffle, 5 is a Guide rail, 6 is a base, 7 is a bottom platform, 8 is a cylinder, 9 is a model support, 10 is a guide rail slider, and 11 is a cylinder joint.
[0027] Such as figure 1 , 2 As shown, the model 1 (for the rudder surface model or the airfoil model) is installed on the model support 9, and the rudder shaft support form of the rudder surface model 1 or the airfoil model 1 is realized by installing different clamps on the model support 9. The form of root support is described below by taking the rudder surface model as an example.
[0028] The rudder surface model 1 is not connected with the reflector 3 and there is a suitable gap between the reflector 3 and the reflector 3 . The reflector 3 provides the root flow fi...
PUM
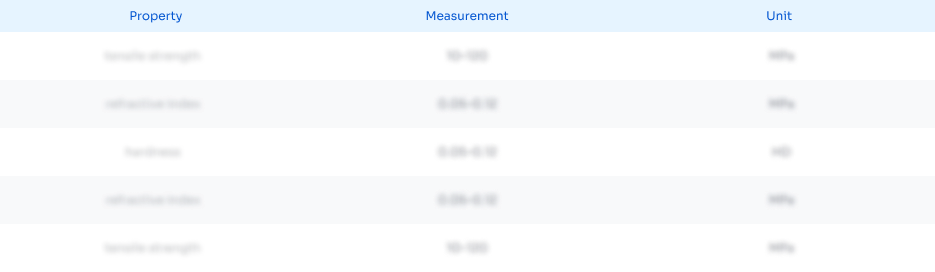
Abstract
Description
Claims
Application Information

- R&D
- Intellectual Property
- Life Sciences
- Materials
- Tech Scout
- Unparalleled Data Quality
- Higher Quality Content
- 60% Fewer Hallucinations
Browse by: Latest US Patents, China's latest patents, Technical Efficacy Thesaurus, Application Domain, Technology Topic, Popular Technical Reports.
© 2025 PatSnap. All rights reserved.Legal|Privacy policy|Modern Slavery Act Transparency Statement|Sitemap|About US| Contact US: help@patsnap.com