Thrust distribution method for magnetic levitation planar motor
A planar motor and thrust distribution technology, applied in the direction of non-rotational vibration suppression, etc., can solve the problems affecting the dynamic quality of the motion table, not being able to meet the nanometer and sub-nanometer precision, affecting the positioning and motion precision and the stability of the control system, etc.
- Summary
- Abstract
- Description
- Claims
- Application Information
AI Technical Summary
Problems solved by technology
Method used
Image
Examples
Embodiment Construction
[0055] The specific embodiment of the present invention is described in further detail below in conjunction with accompanying drawing,
[0056] figure 1 It is a structural schematic diagram of the magnetic levitation planar motor of the present invention, figure 2 It is a flowchart of the method of the present invention, the magnetic levitation planar motor 100 includes a first voice coil motor 101 , a second voice coil motor 102 , a third voice coil motor 103 and a fourth voice coil motor 104 . When the four voice coil motors are energized, they will generate thrust to drive the magnetic levitation planar motor to complete rotation around the X axis, rotation around the Y axis and translation in the Z direction to achieve vertical three-degree-of-freedom motion.
[0057] The object of the present invention is to provide a method for distributing thrust of a magnetic levitation planar motor, which is used to effectively suppress the flexible vibration of the magnetic levitat...
PUM
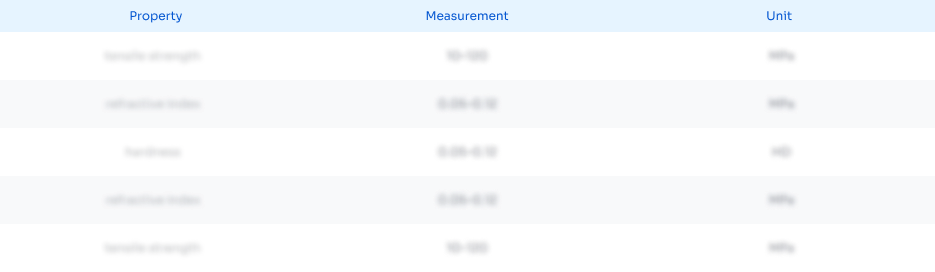
Abstract
Description
Claims
Application Information

- R&D Engineer
- R&D Manager
- IP Professional
- Industry Leading Data Capabilities
- Powerful AI technology
- Patent DNA Extraction
Browse by: Latest US Patents, China's latest patents, Technical Efficacy Thesaurus, Application Domain, Technology Topic, Popular Technical Reports.
© 2024 PatSnap. All rights reserved.Legal|Privacy policy|Modern Slavery Act Transparency Statement|Sitemap|About US| Contact US: help@patsnap.com