Loose fiber dyeing process
A loose fiber and process technology, which is applied in the field of loose fiber dyeing technology, can solve the problems that affect the loosening of loose fibers, large water consumption, uneven distribution of loose fibers, etc., to avoid insufficient fiber opening, stabilize transportation, and strengthen uniform distribution Effect
- Summary
- Abstract
- Description
- Claims
- Application Information
AI Technical Summary
Problems solved by technology
Method used
Image
Examples
Embodiment 1
[0036] The bulk fiber dyeing process of this embodiment includes the following steps of catching cotton, forming a net, soaking liquid, squeezing liquid, forming coils, cold stacking, unwinding, washing, rolling water, opening fibers and drying, grasping cotton, forming a net , immersion, cold stacking, washing, water rolling after the loose fiber web is opened and then dried in the form of loose fibers. The implementation process in this embodiment can refer to figure 1 , including cotton grabbing device 1, web forming device 2, liquid soaking device 3, liquid squeezing device 4, coil forming device 5, cold stack color fixing device 6, uncoiling device 7, water washing device 8, water squeezing device 9 installed in sequence , fiber opening device 10 and drying device 12, a feeding belt (feeding belt one 100) is set between the water rolling device 9 and the fiber opening device 10, and the loose fiber web after water rolling is sent to the fiber opening device place for fiber...
Embodiment 2
[0042] The bulk fiber dyeing process of this embodiment includes the following steps of catching cotton, forming a net, soaking liquid, squeezing liquid, forming coils, cold stacking, unwinding, washing, rolling water, opening fibers and drying, grasping cotton, forming a net , immersion, cold stacking, washing, water rolling, and after pre-opening and fine-fibering treatment, the loose fiber web is dried in the form of loose fibers. The implementation process in this embodiment can refer to figure 2 , including cotton grabbing device 1, web forming device 2, liquid soaking device 3, liquid squeezing device 4, coil forming device 5, cold stack color fixing device 6, uncoiling device 7, water washing device 8, water squeezing device 9 installed in sequence , fiber opening device 10 and drying device 12, a feeding belt 100 is set between the water rolling device 9 and the fiber opening device 10, and the loose fiber web after water rolling is sent to the fiber opening device pla...
Embodiment 3
[0048] The bulk fiber dyeing process of this embodiment includes the steps of grasping cotton, forming a net, soaking liquid, rolling liquid, coiling, cold stacking, unwinding, washing, rolling water, opening fiber, laying fiber and drying in sequence. , netting, immersion, cold stacking, washing, water rolling, the loose fiber web is pre-opened and finely opened, and the loose fiber is dried after the fiber laying treatment. The implementation process in this embodiment can be refer to image 3 with Figure 4, including cotton grabbing device 1, web forming device 2, liquid soaking device 3, liquid squeezing device 4, coil forming device 5, cold stack color fixing device 6, uncoiling device 7, water washing device 8, water squeezing device 9 installed in sequence , fiber opening device 10, fiber laying device 11 and drying device 12, feeding belt 100 is set between water rolling device 9 and fiber opening device 10, fiber laying device 11 is arranged between fiber opening de...
PUM
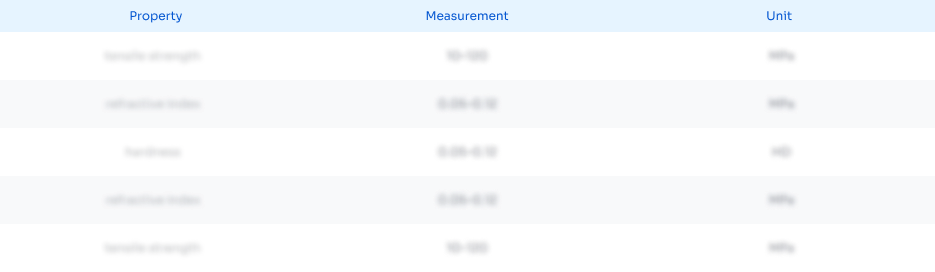
Abstract
Description
Claims
Application Information

- Generate Ideas
- Intellectual Property
- Life Sciences
- Materials
- Tech Scout
- Unparalleled Data Quality
- Higher Quality Content
- 60% Fewer Hallucinations
Browse by: Latest US Patents, China's latest patents, Technical Efficacy Thesaurus, Application Domain, Technology Topic, Popular Technical Reports.
© 2025 PatSnap. All rights reserved.Legal|Privacy policy|Modern Slavery Act Transparency Statement|Sitemap|About US| Contact US: help@patsnap.com