600MPa hot-rolled ribbed steel bar and preparation method thereof
A hot-rolled ribbed steel bar and steel bar technology, applied in the field of low-alloy steel production, can solve problems such as difficult large-scale application, affecting the quality of finished products, and high performance requirements of rolling mills, so as to reduce alloy content, reduce production costs, and improve steel bar strength. Effect
- Summary
- Abstract
- Description
- Claims
- Application Information
AI Technical Summary
Problems solved by technology
Method used
Image
Examples
Embodiment 1
[0025] Prepare a 600MPa hot-rolled ribbed steel bar with a diameter of 12mm. The chemical composition of molten steel is calculated by weight percentage: C: 0.068%, Si: 0.2%, Mn: 1.45%, P: 0.04%, S: 0.04%, B: 0.0034%, Nb: 0.03%, V: 0.027%, Ti: 0.011, N: 0.005%;
[0026] Its preparation method includes the steps of molten iron desulfurization, converter smelting, nitrogen blowing, continuous casting, billet heating, rolling, controlled cooling, and cooling bed air cooling, wherein,
[0027] The hot metal desulfurization adopts the magnesium powder desulfurization process, and the sulfur content of the outgoing hot metal is controlled to be S≤0.040%, and the desulfurization slag in the tank is cleaned;
[0028] During converter smelting, the amount of steel scrap charged accounts for 10% of the total charge; the converter adopts top-bottom composite blowing, and the end point adopts high-drawing supplementary blowing process; the final slag basicity target is 3.6; the converter ...
Embodiment 2
[0034] Prepare a 600MPa hot-rolled ribbed steel bar with a diameter of 18mm. The chemical composition of molten steel is calculated by weight percentage: C: 0.083%, Si: 0.35%, Mn: 1.36%, P: 0.034%, S: 0.022%, B: 0.0027%, Nb: 0.041%, V: 0.043%, Ti: 0.035, N: 0.0085%;
[0035] The preparation method includes the steps of molten iron desulfurization, converter smelting, nitrogen blowing, continuous casting, billet heating, rolling, controlled cooling, and cooling bed air cooling, wherein:
[0036] The hot metal desulfurization adopts the magnesium powder desulfurization process, and the sulfur content of the outgoing hot metal is controlled to S≤0.040%, and the desulfurization slag in the tank is cleaned
[0037] During converter smelting, the scrap load accounts for 12% of the total load; the converter adopts top-bottom compound blowing, and the end point adopts high-drawing supplementary blowing process; the final slag basicity target is 3.2; the converter end point C control w...
Embodiment 3
[0043] Prepare a 600MPa hot-rolled ribbed steel bar with a diameter of 28mm. The chemical composition of molten steel is calculated by weight percentage: C: 0.13%, Si: 0.41%, Mn: 1.47%, P: 0.032%, S: 0.027%, B: 0.002%, Nb: 0.042%, V: 0.041%, Ti: 0.018, N: 0.005%;
[0044] Its preparation method includes the steps of molten iron desulfurization, converter smelting, nitrogen blowing, continuous casting, billet heating, rolling, controlled cooling, and cooling bed air cooling, wherein,
[0045] The hot metal desulfurization adopts the magnesium powder desulfurization process, and the sulfur content of the outgoing hot metal is controlled to be S≤0.040%, and the desulfurization slag in the tank is cleaned;
[0046] During converter smelting, the amount of steel scrap loaded accounts for 13% of the total amount loaded; the converter adopts top-bottom composite blowing, and the end point adopts a high-drawing supplementary blowing process; the final slag basicity target is 2.8; the ...
PUM
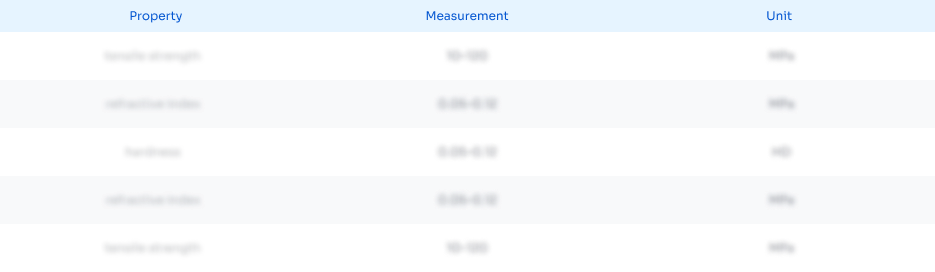
Abstract
Description
Claims
Application Information

- R&D Engineer
- R&D Manager
- IP Professional
- Industry Leading Data Capabilities
- Powerful AI technology
- Patent DNA Extraction
Browse by: Latest US Patents, China's latest patents, Technical Efficacy Thesaurus, Application Domain, Technology Topic, Popular Technical Reports.
© 2024 PatSnap. All rights reserved.Legal|Privacy policy|Modern Slavery Act Transparency Statement|Sitemap|About US| Contact US: help@patsnap.com