Graphite electrode and method for steel pipe inner diameter machining with graphite electrode
A technology for graphite electrodes and steel pipes, applied in the direction of electric processing equipment, electrochemical processing equipment, processing electrodes, etc., can solve partial wall or elliptical protrusions, cannot meet the accuracy and uniformity of stainless steel pipes, and cannot be turned to process the inner diameter of steel pipes And other problems, to achieve high work efficiency, very economical effect
- Summary
- Abstract
- Description
- Claims
- Application Information
AI Technical Summary
Problems solved by technology
Method used
Image
Examples
Embodiment Construction
[0029] see figure 1 , a graphite electrode 1, comprising an insulating shell 11, a connecting cable 12, an insulating receiving plate 13, a graphite electrode tip 14 and at least one exhaust unit 15; the insulating shell 11 is fixedly connected to the top of the insulating receiving plate 13 ; One end of the connecting cable 12 passes through the insulating shell 11 and is electrically connected to the graphite electrode head 14; the connecting cable 12 is used for connecting the graphite electrode 1 to a DC power supply.
[0030] see again figure 1 , the longitudinal axis of the insulating receiving plate 13 is provided with a rotary hole 131, and the lower ring of the inner wall of the rotary hole 131 is provided with a plurality of first threads (not shown); that is, the rotary hole 131 is a two-stage stepped hole, The first thread is provided on the inner wall of the large hole 1311 of the stepped hole, and the top end of the connecting portion 141 described below can abu...
PUM
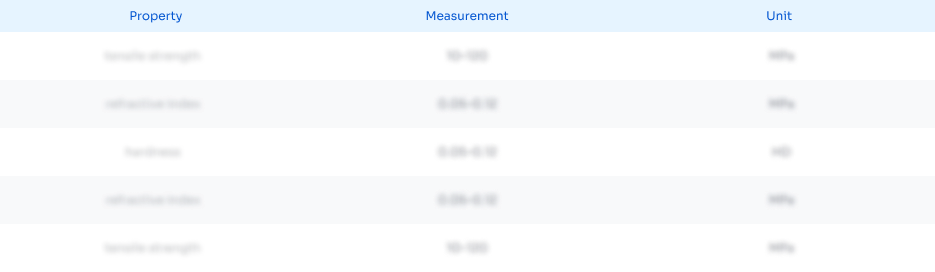
Abstract
Description
Claims
Application Information

- Generate Ideas
- Intellectual Property
- Life Sciences
- Materials
- Tech Scout
- Unparalleled Data Quality
- Higher Quality Content
- 60% Fewer Hallucinations
Browse by: Latest US Patents, China's latest patents, Technical Efficacy Thesaurus, Application Domain, Technology Topic, Popular Technical Reports.
© 2025 PatSnap. All rights reserved.Legal|Privacy policy|Modern Slavery Act Transparency Statement|Sitemap|About US| Contact US: help@patsnap.com