Technical method for preparing aromatic hydrocarbon through methanol aromatization
A process method and aromatization technology, which are applied in the field of aromatic hydrocarbon production and chemical industry, can solve the problems of lack of comprehensive utilization and low conversion rate of non-aromatic liquid phase products, and achieve the improvement of total yield, reduction of aromatic hydrocarbon separation difficulty, and high methanol conversion rate. and the effect of aromatic selectivity
- Summary
- Abstract
- Description
- Claims
- Application Information
AI Technical Summary
Problems solved by technology
Method used
Image
Examples
Embodiment 1
[0031] The catalyst for methanol alkylation is Zn-ZSM-5 nanometer molecular sieve catalyst (the silicon-aluminum ratio of ZSM-5 molecular sieve is 35, and the loading capacity of ZnO is 4.0wt%), and the catalyst for olefin aromatization is nanometer ZSM-5 modified by hydrothermal treatment. Molecular sieve catalyst (the silicon-aluminum ratio of ZSM-5 molecular sieve is 50). The process conditions for the aromatization of methanol and olefins are: the reaction pressure is 0.5MPa, the temperature is 420°C, and the mass space velocity of methanol is 1.0h -1 . The PONA composition of the product after methanol and olefin aromatization reaction is shown in Table 1.
[0032] The product of methanol and olefin aromatization reactor enters the non-aromatic cracking reactor equipped with Ni-ZSM-5 molecular sieve catalyst (the loading capacity of NiO is 2.0wt%) for reaction. The process conditions of non-aromatic cracking are: reaction pressure 0.5MPa, temperature is 360℃, mass space...
Embodiment 2
[0040] The catalyst for methanol alkylation is Zn-ZSM-5 nanometer molecular sieve catalyst (the silicon-aluminum ratio of ZSM-5 molecular sieve is 35, and the loading capacity of ZnO is 4.0wt%), and the catalyst for olefin aromatization is nanometer ZSM-5 modified by hydrothermal treatment. Molecular sieve catalyst (the silicon-aluminum ratio of ZSM-5 molecular sieve is 50). The process conditions for the aromatization of methanol and olefins are: the reaction pressure is 0.1MPa, the temperature is 380°C, and the mass space velocity of methanol is 0.5h -1 .
[0041] The product of methanol and olefin aromatization reactor enters the non-aromatic cracking reactor equipped with Ni-ZSM-5 molecular sieve catalyst (the loading capacity of NiO is 2.0wt%) for reaction. The process conditions of non-aromatic cracking are: reaction pressure 0.1MPa, temperature is 360℃, mass space velocity is 0.5h -1 . After the product is separated by an oil-water separator, a deethanizer and a dehe...
Embodiment 3
[0044] Methanol hydrocarbonization catalyst adopts Ga-Zn-ZSM-5 nano-molecular sieve catalyst (the silicon-aluminum ratio of ZSM-5 molecular sieve is 35, Ga 2 o 3 The loading amount is 1.0wt%, and the loading amount of ZnO is 3.0wt%), and the olefin aromatization catalyst is a nano ZSM-5 molecular sieve catalyst modified by hydrothermal treatment (the silicon-aluminum ratio of the ZSM-5 molecular sieve is 50). The process conditions for the aromatization of methanol and olefins are: the reaction pressure is 0.5MPa, the temperature is 420°C, and the mass space velocity of methanol is 1.0h -1 .
[0045] The product of methanol and olefin aromatization reactor enters the non-aromatic cracking reactor equipped with Ni-ZSM-5 molecular sieve catalyst (the loading capacity of NiO is 3.0wt%) for reaction. The process conditions of non-aromatic cracking are: reaction pressure 0.5MPa, temperature 380℃, mass space velocity 1.0h -1 . After the product is separated by an oil-water separ...
PUM
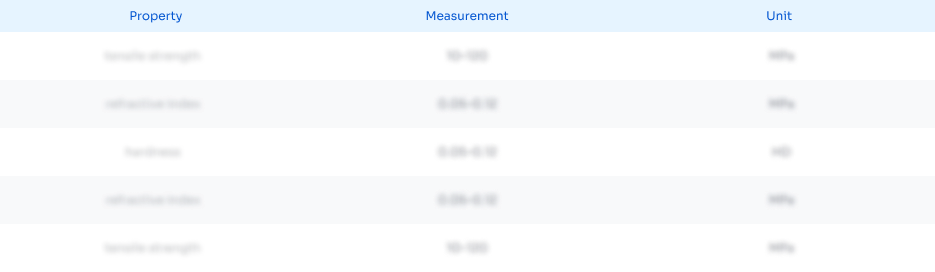
Abstract
Description
Claims
Application Information

- R&D
- Intellectual Property
- Life Sciences
- Materials
- Tech Scout
- Unparalleled Data Quality
- Higher Quality Content
- 60% Fewer Hallucinations
Browse by: Latest US Patents, China's latest patents, Technical Efficacy Thesaurus, Application Domain, Technology Topic, Popular Technical Reports.
© 2025 PatSnap. All rights reserved.Legal|Privacy policy|Modern Slavery Act Transparency Statement|Sitemap|About US| Contact US: help@patsnap.com