Alkane dehydrogenation sulfide catalyst and alkane dehydrogenation method
A technology for alkane dehydrogenation and catalysts, applied in the direction of physical/chemical process catalysts, hydrocarbons, hydrocarbons, etc., to achieve high yield, slow deactivation, and low price
- Summary
- Abstract
- Description
- Claims
- Application Information
AI Technical Summary
Problems solved by technology
Method used
Image
Examples
Embodiment 1
[0031] Add 529.4 g of deionized water to 132.4 g of pseudoboehmite, stir well in a water bath at 80° C., add hydrochloric acid to form a gel, and adjust the pH value to about 3. Weigh the nickel sulfate (Ni(SO) of 31.8g 4 ) 2 ·6H 2 O) Add to the prepared gel, add 50g of deionized water, stir evenly, dry at 120°C for 8h, then roast at 600°C for 12h, finally grind and sieve to get 80-180 mesh particles for later use. During the reaction process, in order to maintain the sulfide state of the active components of the catalyst, 300 μg / g (calculated as sulfur element) hydrogen sulfide is introduced into the feed and transported to the catalyst bed along with the raw materials. The catalyst evaluation results showed that the conversion rate of isobutane was 70.48wt%, the yield of isobutene was 56.31wt%, and the selectivity of isobutene was 79.89wt%.
Embodiment 2
[0033] Weigh 90g silicon oxide (SiO 2 ) as a carrier, 50.5g iron nitrate (Fe(NO 3 ) 3 9H 2 O) Dissolve in 80g deionized water and stir well. Impregnated Fe(NO 3 ) 3 solution, dried at 140°C for 10h, then weighed 13.8g of ammonium sulfate ((NH 4 ) 2 SO 4 ) was dissolved in water, impregnated on the catalyst, dried at 140°C for 8h, and then calcined at 600°C for 12h. During the reaction process, in order to maintain the vulcanized state of the active components of the catalyst, 250 μg / g (calculated as elemental sulfur) of sulfur dioxide is introduced into the feed and transported to the catalyst bed along with the raw materials. The catalyst evaluation results showed that the conversion rate of isobutane was 47.60wt%, the yield of isobutene was 40.88wt%, and the selectivity of isobutene was 85.89wt%.
Embodiment 3
[0035] Weigh 90g zirconia (ZrO 2 ) as a carrier, 35.1g cobalt nitrate (Co(NO 3 ) 2 ·6H 2 O) Dissolve in 80g deionized water and stir well. Co(NO) impregnated on zirconia 3 ) 2 solution, dried at 140°C for 9h, then weighed 10.2g of sulfuric acid (H 2 SO 4 ) and diluted, impregnated on the catalyst, dried at 140°C for 10h, and then calcined at 600°C for 12h. During the reaction process, in order to maintain the sulfidation state of the active components of the catalyst, 300 μg / g (calculated as sulfur element) carbon disulfide is introduced into the feed and transported to the catalyst bed along with the raw materials. The catalyst evaluation results showed that the conversion rate of isobutane was 47.79wt%, the yield of isobutene was 41.90wt%, and the selectivity of isobutene was 87.69wt%.
PUM
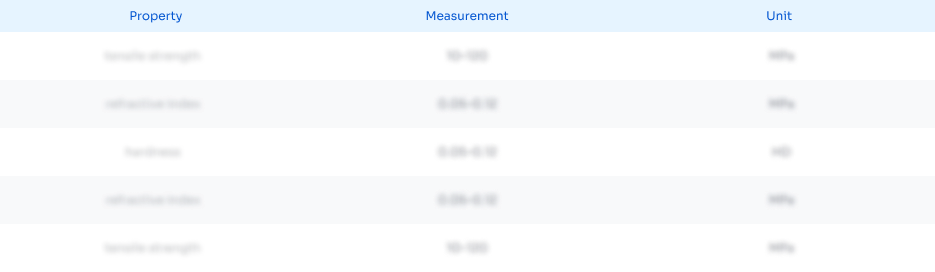
Abstract
Description
Claims
Application Information

- Generate Ideas
- Intellectual Property
- Life Sciences
- Materials
- Tech Scout
- Unparalleled Data Quality
- Higher Quality Content
- 60% Fewer Hallucinations
Browse by: Latest US Patents, China's latest patents, Technical Efficacy Thesaurus, Application Domain, Technology Topic, Popular Technical Reports.
© 2025 PatSnap. All rights reserved.Legal|Privacy policy|Modern Slavery Act Transparency Statement|Sitemap|About US| Contact US: help@patsnap.com