Two-stage parallel robot device applied to precision assembly
A robot and parallel technology, applied in the direction of manipulator, program control manipulator, metal processing, etc., can solve the problems of high component quality, small working space of parallel mechanism, poor flexibility, etc., and achieve the effect of strong bearing capacity
- Summary
- Abstract
- Description
- Claims
- Application Information
AI Technical Summary
Problems solved by technology
Method used
Image
Examples
Embodiment Construction
[0020] The implementation of the present invention will be described in detail below in conjunction with the drawings and examples.
[0021] figure 1 A schematic diagram of a two-stage parallel robotic device for precision assembly. The upper cable 1, the cable platform 2, and the lower cable 3 form a 7-cable parallel mechanism. The static platform 2, the dynamic platform 5, and the telescopic legs 6 form a Stewart parallel mechanism. The device is composed of a rope parallel mechanism and a Stewart parallel mechanism. The rope platform 2 of the rope parallel mechanism serves as the static platform of the Stewart parallel mechanism. The assembly workpiece 7 is installed on the moving platform 6, and its pose in space is jointly determined by the rope parallel mechanism and the Stewart parallel mechanism. Under the comprehensive control of the upper cable 1 and the lower cable 3, the cable platform 2 can adjust the pose of the assembly workpiece 7 in a wide range. pose offs...
PUM
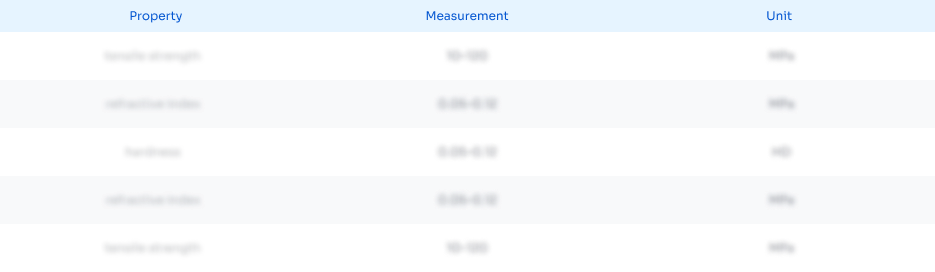
Abstract
Description
Claims
Application Information

- R&D
- Intellectual Property
- Life Sciences
- Materials
- Tech Scout
- Unparalleled Data Quality
- Higher Quality Content
- 60% Fewer Hallucinations
Browse by: Latest US Patents, China's latest patents, Technical Efficacy Thesaurus, Application Domain, Technology Topic, Popular Technical Reports.
© 2025 PatSnap. All rights reserved.Legal|Privacy policy|Modern Slavery Act Transparency Statement|Sitemap|About US| Contact US: help@patsnap.com