Photo-assisted heating system for hydride vapor phase epitaxy
A hydride gas phase, heating system technology, applied in the directions from chemical reactive gases, chemical instruments and methods, single crystal growth, etc. Effect
- Summary
- Abstract
- Description
- Claims
- Application Information
AI Technical Summary
Problems solved by technology
Method used
Image
Examples
Embodiment Construction
[0016] Option 1: If figure 1 , The outer wall 2 of the quartz tube of the vertical HVPE reactor 1 is surrounded by a resistance heater 3 (the resistance heater is generally divided into three or four zones, here simplified as a single zone). On the basis of the resistance heater, an infrared lamp heater 4 is arranged inside the reactor. Arranged directly above the graphite substrate 8 and directly below the shower head 9 . Relying on the infrared lamp 4A and the hemispherical reflector 4B, the radiant light is aimed at the center of the graphite substrate 8 and its surroundings for irradiation, and the central part of the graphite substrate is rapidly heated to compensate for the temperature difference between the center temperature of the graphite disk and the heat at the edge.
[0017] Option 2: If figure 2 , several infrared lamp heaters 5 are evenly arranged outside the reactor 1, around the outer wall 2 of the quartz tube, and at an angle of about 45 degrees above the ...
PUM
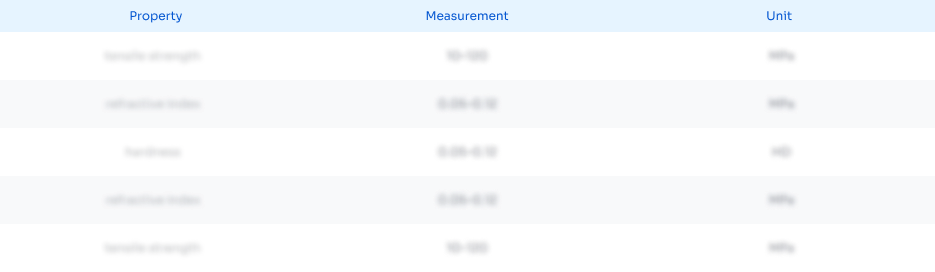
Abstract
Description
Claims
Application Information

- Generate Ideas
- Intellectual Property
- Life Sciences
- Materials
- Tech Scout
- Unparalleled Data Quality
- Higher Quality Content
- 60% Fewer Hallucinations
Browse by: Latest US Patents, China's latest patents, Technical Efficacy Thesaurus, Application Domain, Technology Topic, Popular Technical Reports.
© 2025 PatSnap. All rights reserved.Legal|Privacy policy|Modern Slavery Act Transparency Statement|Sitemap|About US| Contact US: help@patsnap.com