Method for directly preparing light alkene by using synthetic gas as raw material
A low-carbon olefin and synthesis gas technology, which is applied in the preparation of liquid hydrocarbon mixtures and the petroleum industry, can solve the problems of low conversion rate of CO and low selectivity of low-carbon olefins, so as to improve the degree of reduction and the selection of low-carbon olefins properties, and weaken the effect of the secondary reaction of olefins
- Summary
- Abstract
- Description
- Claims
- Application Information
AI Technical Summary
Problems solved by technology
Method used
Image
Examples
Embodiment 1
[0028] The required amount of acid-washed alumina carrier is calcined at 1100° C. for 1 hour for later use. Dissolve the required amount of ferric nitrate, manganese nitrate, magnesium nitrate and potassium nitrate in water to form the mixed solution I with the required proportion concentration. Under vacuum conditions, impregnate the above mixed solution I on the required amount of treated α-alumina carrier to obtain the catalyst precursor J. The impregnated catalyst precursor J was dried at 110°C, and then calcined at a temperature of 600°C for 2 hours to obtain a catalyst for the direct production of low-carbon olefins from synthesis gas. The weight composition of the catalyst was: :
[0029] 20% Fe 100 mn 10 Mg 2.0 K 15 o x +80%Al 2 o 3
[0030] Table 1 shows the experimental results of the direct production of light olefins from syngas as raw material with the prepared catalyst under certain reaction conditions.
[0031]
Embodiment 2
[0033] The required amount of acid-washed alumina carrier is calcined at 900° C. for 1 hour for later use. Dissolve the required amount of ferric nitrate, manganese nitrate, magnesium nitrate and potassium nitrate in water to form the mixed solution I with the required proportion concentration. Under vacuum conditions, impregnate the above mixed solution I on the required amount of treated α-alumina carrier to obtain the catalyst precursor J. The impregnated catalyst precursor J was dried at 110°C, and then calcined at a temperature of 600°C for 2 hours to obtain a catalyst for the direct production of low-carbon olefins from synthesis gas. The weight composition of the catalyst was: :
[0034] 20% Fe 100 mn 50 Sr 40 K 5 o x +80%Al 2 o 3
[0035] Table 1 shows the experimental results of the direct production of light olefins from syngas as raw material with the prepared catalyst under certain reaction conditions.
[0036]
Embodiment 3
[0038] The required amount of acid-washed alumina carrier is calcined at 1200° C. for 1 hour for later use. Dissolve the required amount of ferric nitrate, manganese nitrate, magnesium nitrate and potassium nitrate in water to form the mixed solution I with the required proportion concentration. Under vacuum conditions, impregnate the above mixed solution I on the required amount of treated α-alumina carrier to obtain the catalyst precursor J. The impregnated catalyst precursor J was dried at 110°C, and then calcined at a temperature of 600°C for 2 hours to obtain a catalyst for the direct production of low-carbon olefins from synthesis gas. The weight composition of the catalyst was: :
[0039] 35% Fe 100 Cu 50 Mg 20 Cs 0.5 o x +65%Al 2 o 3
[0040] Table 1 shows the experimental results of the direct production of light olefins from syngas as raw material with the prepared catalyst under certain reaction conditions.
[0041]
PUM
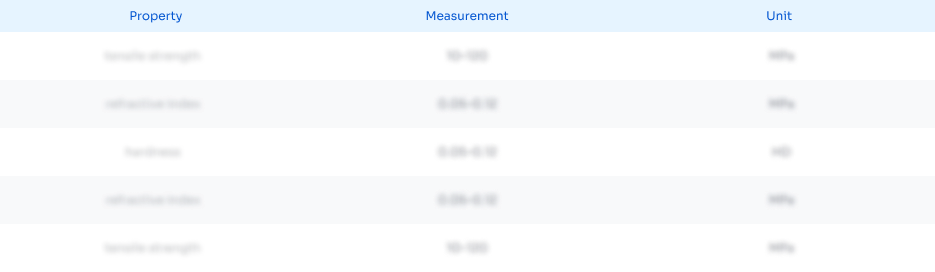
Abstract
Description
Claims
Application Information

- R&D Engineer
- R&D Manager
- IP Professional
- Industry Leading Data Capabilities
- Powerful AI technology
- Patent DNA Extraction
Browse by: Latest US Patents, China's latest patents, Technical Efficacy Thesaurus, Application Domain, Technology Topic, Popular Technical Reports.
© 2024 PatSnap. All rights reserved.Legal|Privacy policy|Modern Slavery Act Transparency Statement|Sitemap|About US| Contact US: help@patsnap.com