Mechanical processing method for dry cylinder liners
A technology of machining and cylinder liner, applied in mechanical equipment, cylinder, cylinder head, etc., can solve the problems of many machining processes, high cost of cylinder liner, large size, etc.
- Summary
- Abstract
- Description
- Claims
- Application Information
AI Technical Summary
Problems solved by technology
Method used
Examples
Embodiment 1
[0016] Embodiment 1: The wall thickness difference of the inner hole of the cylinder liner produced by rough boring is 0.3mm; the dry type cylinder liner is processed according to the following steps:
[0017] (1) Roughly ream the inner hole of the cylinder liner, remove the large margin of the inner hole, and use the inner hole as the positioning reference for the next rough turning outer circle process;
[0018] (2) Roughly turning the outer circle and end face, removing a large margin to prepare for semi-finishing work;
[0019] (3) The margin is removed from the outer circle of the semi-finishing car, and the outer circle is used as the positioning reference for the next fine boring process;
[0020] (4) Fine boring the inner circle to further remove the inner circle allowance;
[0021] (5) Rough honing the inner circle to correct the roundness and straightness of the inner hole to ensure the geometric size and shape accuracy of the next finishing process;
[0022] (6) F...
Embodiment 2
[0027] Embodiment 2: The wall thickness difference of the inner hole of the cylinder liner produced by rough boring is 0.5 mm; the dry type cylinder liner is processed according to the following steps:
[0028] (1) Roughly ream the inner hole of the cylinder liner, remove the large margin of the inner hole, and use the inner hole as the positioning reference for the next rough turning outer circle process;
[0029] (2) Roughly turning the outer circle and end face, removing a large margin to prepare for semi-finishing work;
[0030] (3) The margin is removed from the outer circle of the semi-finishing car, and the outer circle is used as the positioning reference for the next fine boring process;
[0031] (4) Fine boring the inner circle to further remove the inner circle allowance;
[0032] (5) Rough honing the inner circle to correct the roundness and straightness of the inner hole to ensure the geometric size and shape accuracy of the next finishing process;
[0033] (6) ...
PUM
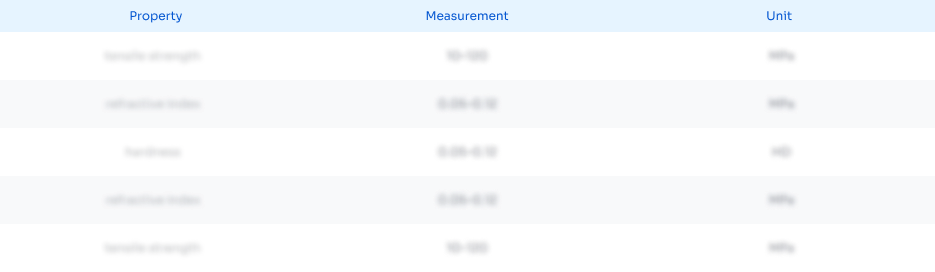
Abstract
Description
Claims
Application Information

- R&D
- Intellectual Property
- Life Sciences
- Materials
- Tech Scout
- Unparalleled Data Quality
- Higher Quality Content
- 60% Fewer Hallucinations
Browse by: Latest US Patents, China's latest patents, Technical Efficacy Thesaurus, Application Domain, Technology Topic, Popular Technical Reports.
© 2025 PatSnap. All rights reserved.Legal|Privacy policy|Modern Slavery Act Transparency Statement|Sitemap|About US| Contact US: help@patsnap.com