Manufacturing method for N-shaped GaAs substrate laser diode
A technology of laser diode and manufacturing method, which is applied to lasers, laser parts, semiconductor lasers, etc., can solve the problems of crystal strain, degradation of the quality and performance of epitaxial layers on substrates, and shortened life of laser diodes, etc.
- Summary
- Abstract
- Description
- Claims
- Application Information
AI Technical Summary
Problems solved by technology
Method used
Image
Examples
Embodiment Construction
[0016] The present invention will be described in detail below in conjunction with the accompanying drawings and specific embodiments, but not as a limitation of the present invention.
[0017] figure 1 A schematic diagram of the structure of the laser diode of the present invention is shown. It includes an n-GaAs substrate 1, on which an n-type cladding layer 2, an n-type light guide layer 3 and an active layer 4 are deposited in sequence.
[0018] The n-type cladding layer 2 is n-Al a In b Ga 1-a-b N, the optical guiding layer 3 is n-Al c In d Ga 1-c-d N, where 0≤a, b, c, d, a+b, c+d≤1.
[0019] The cladding layer 2 can also be n-Al a In b Ga 1-a-b N superlattice.
[0020] Active layer 4 is n-Al with superlattice structure e In f Ga 1-e-f N / n-AI g In h Ga 1-g-h N multiple quantum well layers, where 0≤e, f, g, h, e+f, g+h≤1.
[0021] A p-type barrier layer 5 is also deposited on the active layer 4, and the p-type barrier layer 5 is p-Al i In j Ga 1-i-j N,...
PUM
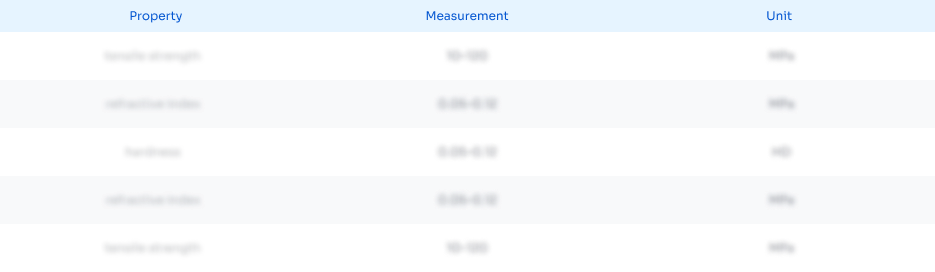
Abstract
Description
Claims
Application Information

- Generate Ideas
- Intellectual Property
- Life Sciences
- Materials
- Tech Scout
- Unparalleled Data Quality
- Higher Quality Content
- 60% Fewer Hallucinations
Browse by: Latest US Patents, China's latest patents, Technical Efficacy Thesaurus, Application Domain, Technology Topic, Popular Technical Reports.
© 2025 PatSnap. All rights reserved.Legal|Privacy policy|Modern Slavery Act Transparency Statement|Sitemap|About US| Contact US: help@patsnap.com